Whether and how the service life of hydraulic hose lines can be extended is a frequent topic of discussion and consultation. However, due to the complexity of the various influencing factors and their impacts, it is impossible to calculate the actual service life of a hydraulic hose line. It isn't possible to make generalised statements. However, the ways in which service life can be optimised are often similar. This article highlights five key areas of action.
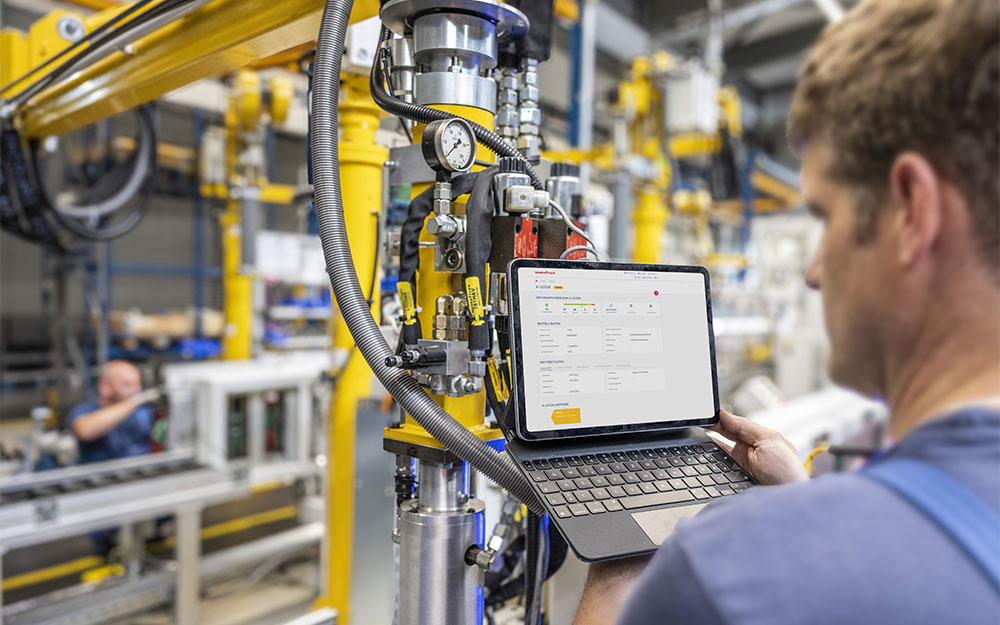
1. Selection and design
The first step is to record and check the data of the hydraulic hose line in question. Is it a brand-name product? Is the hose line manufactured according to the latest technological standards? Is the combination of hose and fitting the right one? In a second step, it must be checked whether the hydraulic hose line is designed to suit the machine or system data. Both ongoing operational requirements and temporary peaks must be taken into account. For example, has the ideal nominal diameter been selected, or would the volume flow be too high? Do the system pressure and pressure peaks as well as any bending radii match the selected hose line material? In particular, the combination of frequent and strong pressure pulses often requires the use of significantly more resistant premium hose lines which considerably exceed the requirements of the relevant hose line standards, for example with regard to pressure pulse tests in accordance with ISO 6803. Constant use at the very limits of the material’s capacity can also lead to premature ageing and failure. If, for example, the system pressure is 200 bar, the hose line should not be designed for a maximum pressure of 200 bar. Instead, you should select a higher-quality hose which is approved for 225 or 250 bar.
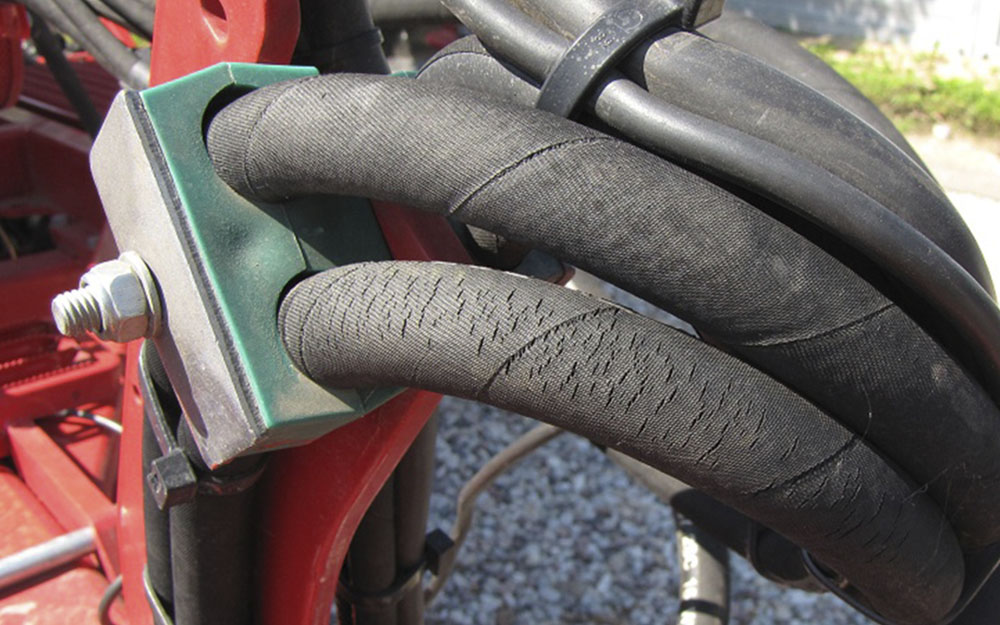
2. Installation situation
Bending radii that are too tight or twisted hose lines are often the cause of short service lives. When checking the installation of hydraulic hose lines in machines and systems, the specifications and recommendations of the relevant standards and regulations must be observed. First and foremost, DIN 20066 and DGUV (German Social Accident Insurance) 113-020 must be complied with. Important: the specifications of the hose line manufacturer, which are outlined in the data sheets, are decisive when it comes to the permissible bending radii. Here too, the recommendation is not to use hose lines at the limit of their capacity - e.g. with the smallest possible bending radius - but to choose products that offer a suitable safety margin. A further factor for ensuring the long service life of hydraulic elements subject to movement is appropriate protection against chafing or kinking.
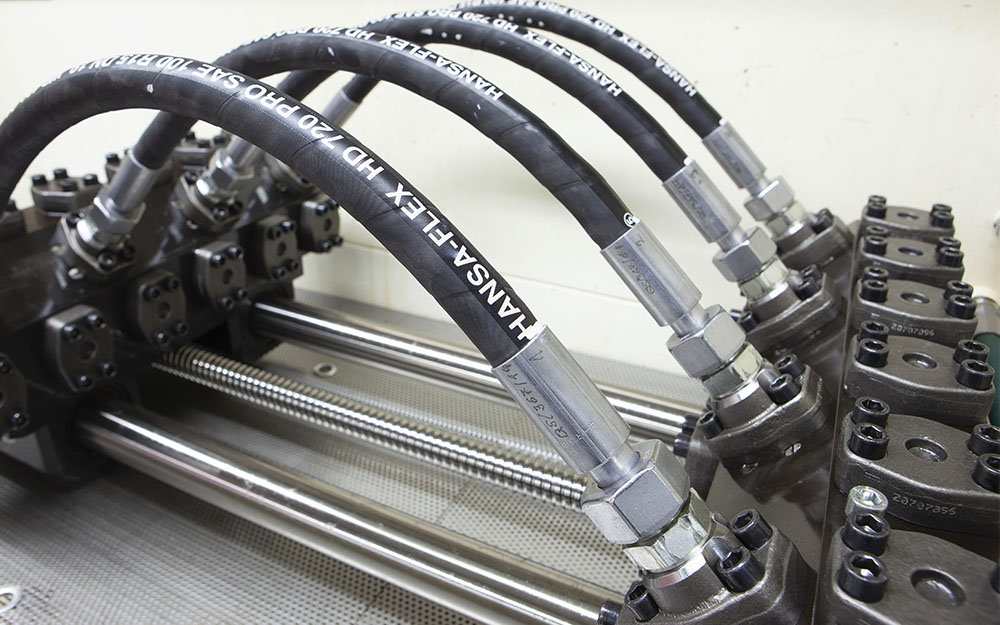
3. Environmental impacts
External environmental influences have a direct impact on the service life of hydraulic hose lines. For example, construction machinery that is used outdoors should be equipped with ozone and UV-resistant hose lines, in order to avoid cracks in the cover of the hose and thus the risk of failure. In addition to UV radiation and ozone, other external factors that need to be taken into account are the ambient temperature, vapour, dust and any aggressive liquids in the operating area. HANSA‑FLEX offers a wide range of hose line types that are precisely designed for use in demanding conditions, and therefore have a longer service life than standard hose lines.

4. Oil quality
The quality of the hydraulic oil used plays an important and often underestimated role. Contaminants such as water, dust and other particles in the hydraulic circuit as well as old, mixed hydraulic fluids that are not used in accordance with the applicable specifications can have a significant impact on the service life of a hose line. For example, used oil based on biological substances can develop acids that can attack a hose line from the inside. It is also important to check whether the oil temperature matches the specifications of the hose line. Oil analyses show possible problem areas as well as possible solutions for improving the oil quality.
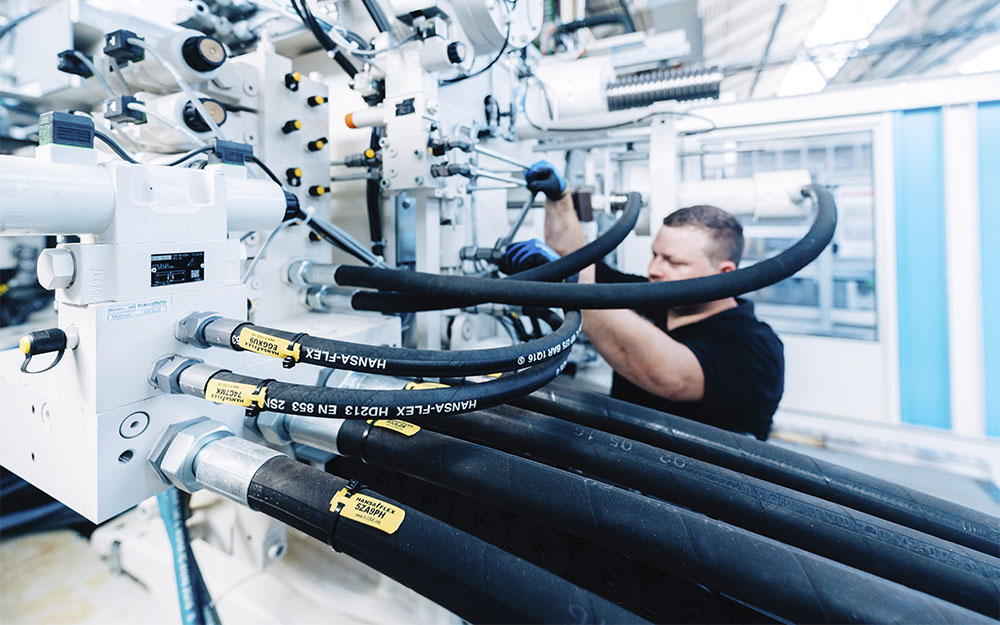
5. Hose line management
Professional hose line management - for example using the My.HANSA‑FLEX online portal - enables well-organised management of all hose lines in use, as well as monitoring and documentation of machine and system-specific maintenance intervals. Abnormalities such as the above-average replacement frequency of a hose line can then be seen at a glance.
Conclusion
If the above points are observed, the basis for a long service life has been created. High-quality hydraulic hose lines can tolerate a number of faults. Several factors often have to come together to cause premature failure. HANSA‑FLEX offers a range of services to improve the service life of hydraulic hose lines together with the customer. On-site appointments with our hydraulics specialists are essential for an initial assessment. Many sources of error can be identified in this way during an inspection of the machine or system. Further insights can be gained by measuring pressure peaks and volume flow, as well as analysing the hydraulic oil. This is because sometimes the cause of failures is not in the hose lines themselves, but lies elsewhere in the hydraulic circuit.