Since 2017 HANSA‑FLEX Fluid Service has been supporting the RailMaint works in Delitzsch with the overhaul of 54-metre-long DB Cargo automobile transport waggons. Their complex electrohydraulic systems need to be flushed and serviced regularly.
When top-class automobiles are transported by rail, this is often done in closed freight waggons, such as the Hcceerrs 330 four-section, closed double-decker car transport waggons operated by DB Cargo. Thanks to their fully enclosed design, they offer protection from the weather and vandalism. To ensure safety and functionality, the waggons have to be overhauled every six years. RailMaint GmbH carries out the maintenance work on behalf of DB Cargo, and is supported by HANSA‑FLEX as a hydraulics partner. Due to its length of 54 metres the Hcceerrs 330 automobile transport waggon has a particularly high load capacity. However, there are only a few repair workshops in Germany that can handle vehicles of this length without prior dismantling. In Delitzsch around 330 technicians offer a complete range of maintenance and mobile services for rail vehicles. In addition to freight waggons, this covers not only the passenger carriages of local, long-distance, suburban and regional railways, but also their components. What makes the works in Delitzsch special, apart from the generous amount of space available, is the very high level of vertical integration with its own joinery, upholstery, flooring, metalworking and paint shops all on one site.
Components and fluid services from HANSA‑FLEX
RailMaint GmbH, and its Delitzsch works in particular, have been working with HANSA‑FLEX for over ten years. "We know HANSA‑FLEX well, because we have been purchasing hydraulic hose lines from the Landsberg Queis branch for many years now, and their quality is exactly what we’re looking for. HANSA‑FLEX also offers its hose lines with fire protection certification, which is of course important for our customers," says Benjamin Gimpel, Head of Technology at the RailMaint works in Delitzsch. Since 2017 RailMaint Delitzsch has also been working with the HANSA‑FLEX Fluid Service to maintain and service the complex electro-hydraulic system on the type 330 automobile transport waggon. In addition to the regular replacement of hydraulic hose lines, HANSA‑FLEX also carries out the dynamic flushing of hose and pipe lines on the waggons. Fluid Service Manager Felix Marschner is on site for HANSA‑FLEX in Delitzsch. He knows the systems and their challenges inside out. "The pipe lines are up to 50 metres long, but the volume of fluid is relatively small. As the hydraulics are only used during loading and unloading, the system does not flush itself and deposits build up, for example from particles that enter the system when the tank is ventilated close to the track bed," explains Marschner. To make sure there are no breakdowns, HANSA‑FLEX cleans the pipes with a special flushing unit. During the flushing process, a turbulent flow of 70 litres per minute is generated and flushed through even the narrowest pipe lines at a temperature of 40-45 °C and a pressure of up to 80 bar. This loosens and removes all clogged particles. By the end of 2023 the fluid service had already serviced and flushed around 70 freight waggons.
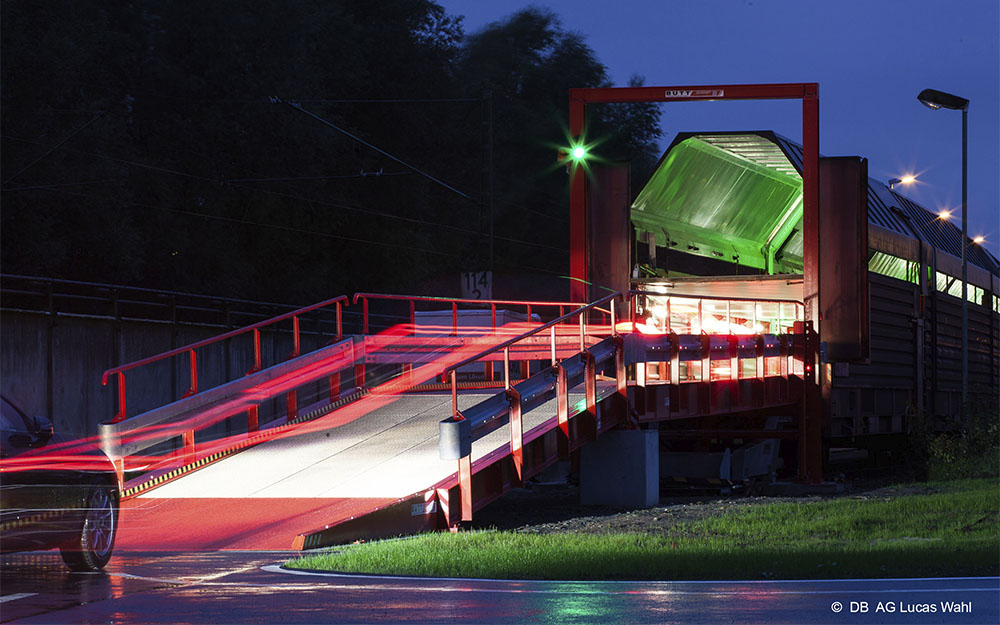
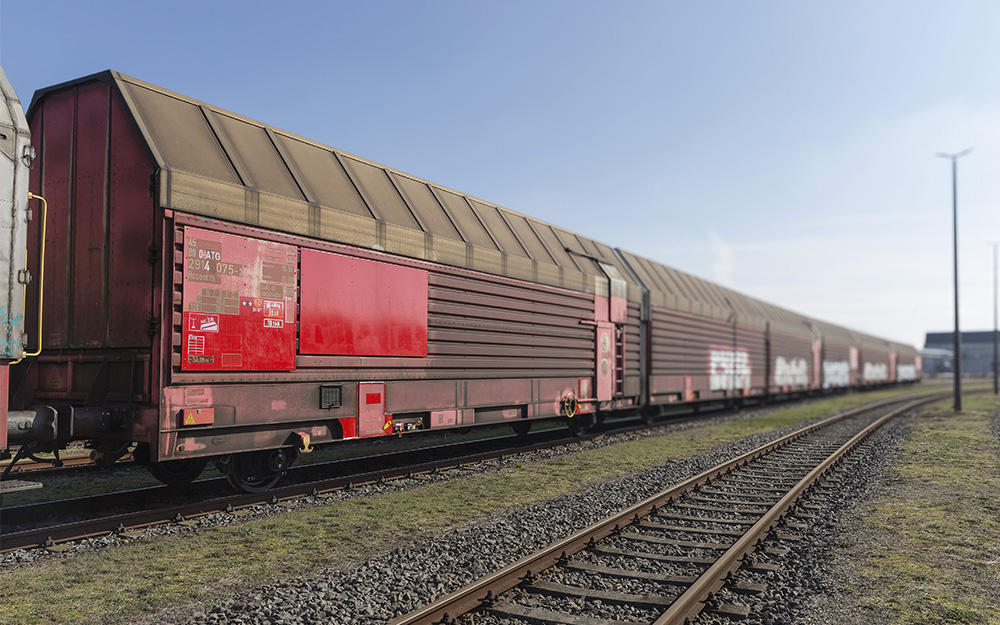
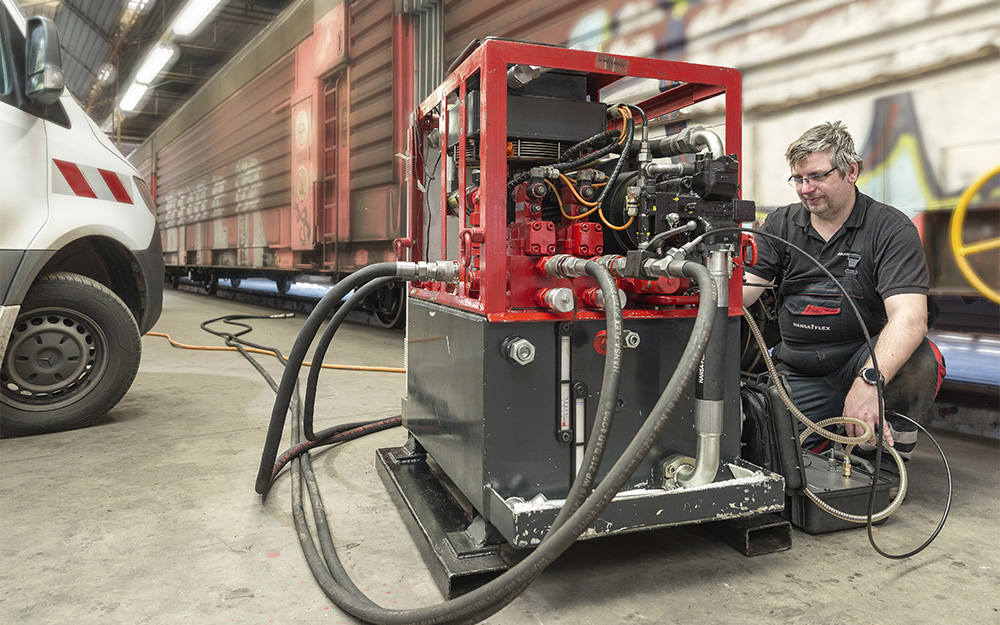
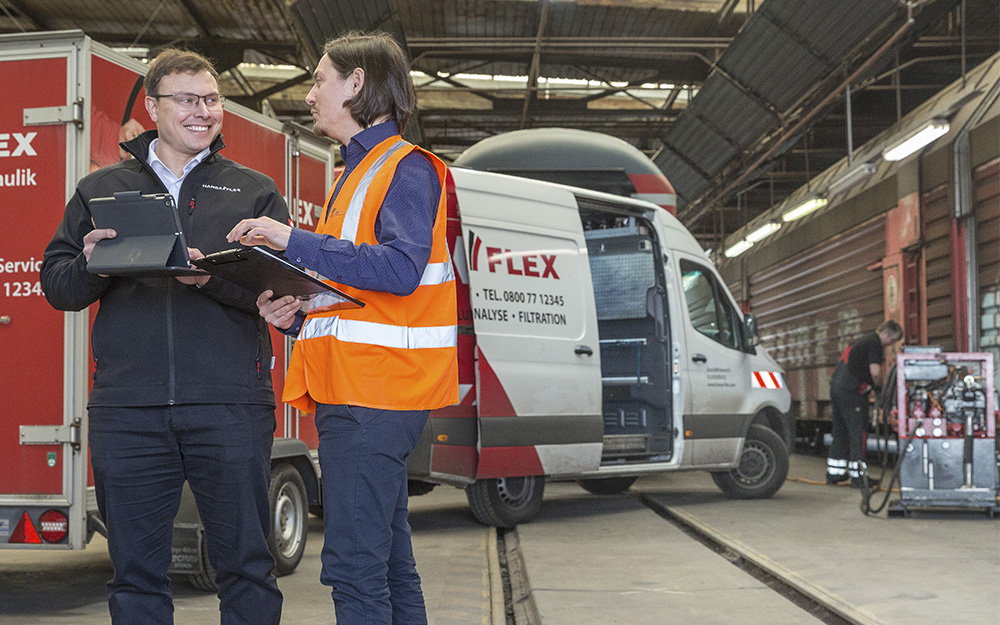
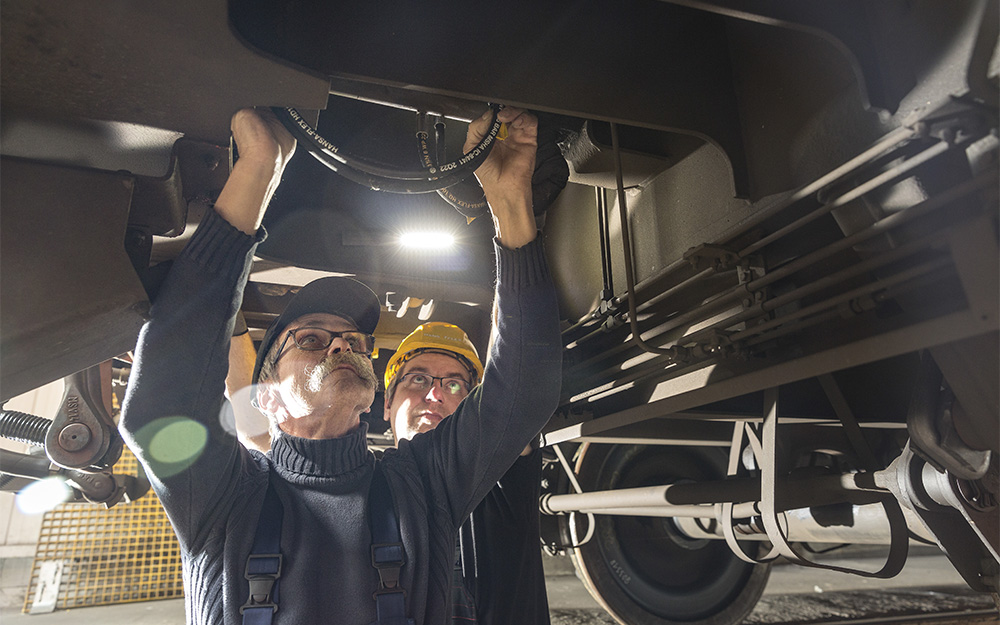
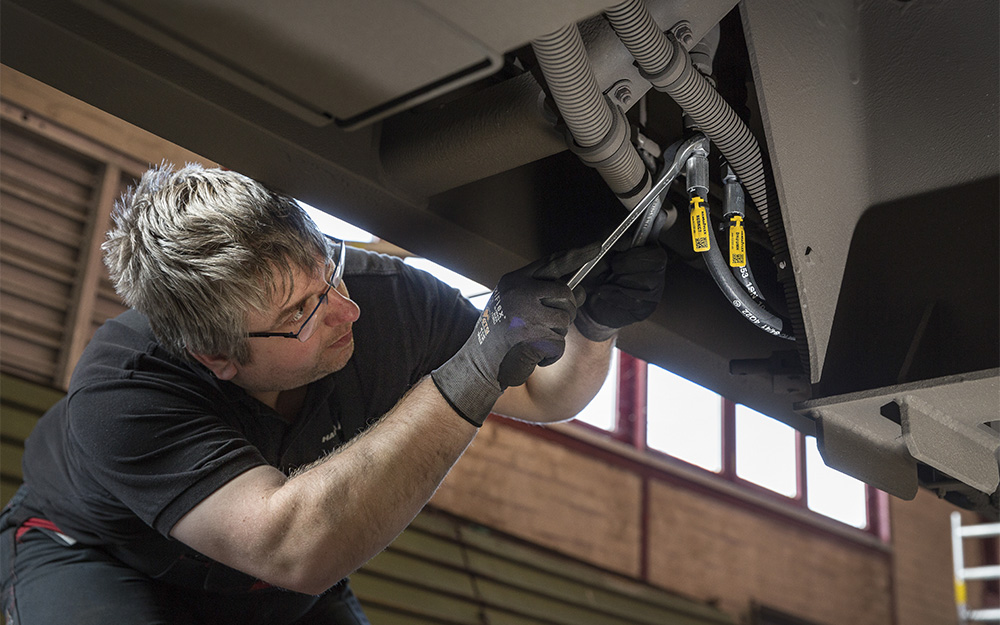
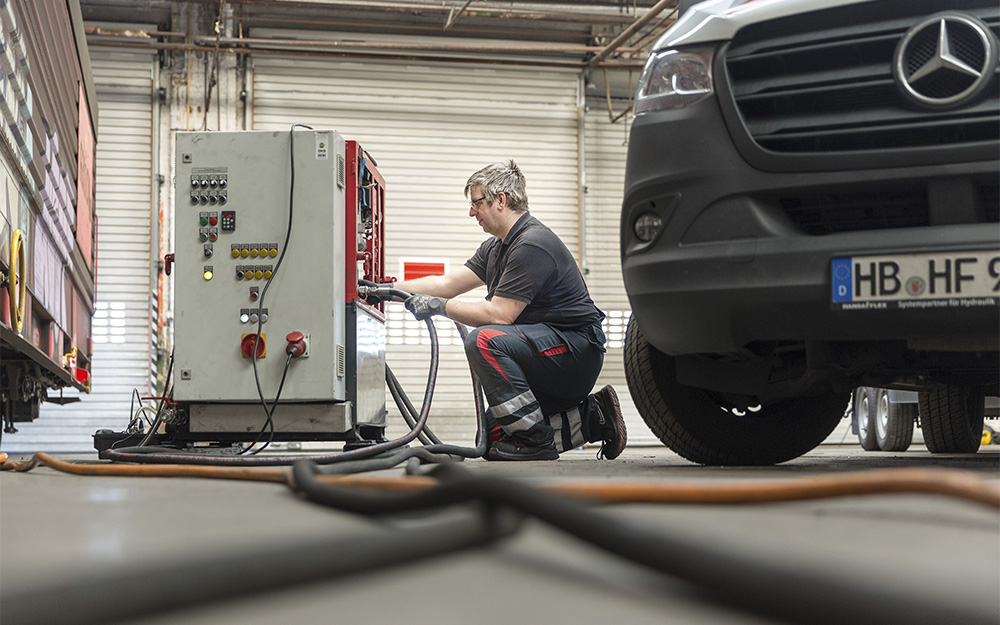
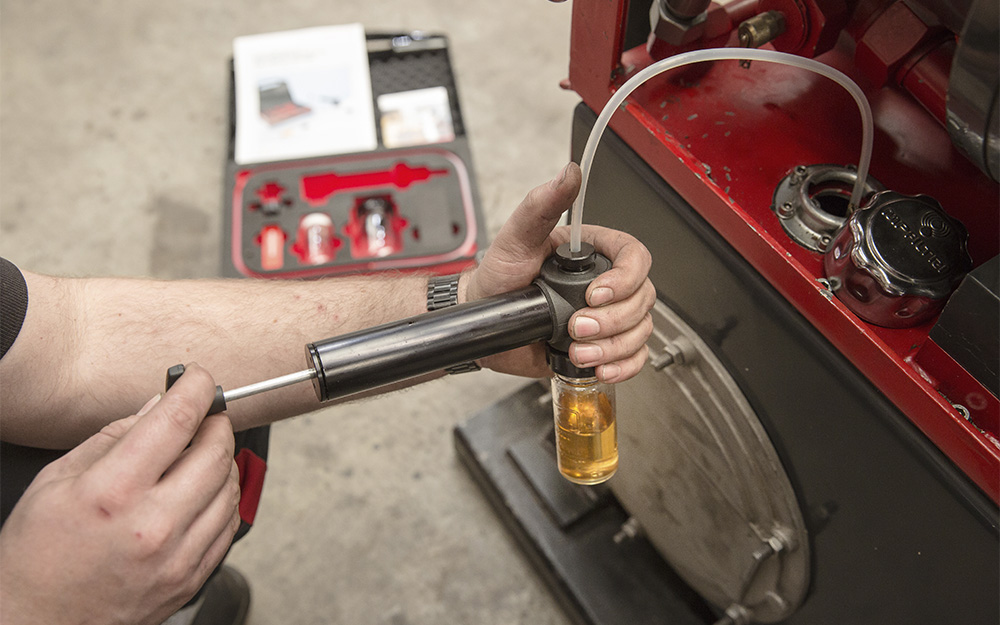
Outstanding cooperation and mutual appreciation
Benjamin Gimpel has warm words for the cooperation with HANSA‑FLEX: "In addition to the product quality, we are also extremely satisfied with the expertise, flexibility and delivery capacity of HANSA‑FLEX. We benefit greatly from the expertise of the HANSA‑FLEX team here on site. They contribute their own ideas, are highly solutions-oriented and know how to identify and tackle problems in a targeted manner." He adds that the reliability of Mr Marschner and his Fluid Service team when it comes to meeting delivery dates also deserves special mention, as does the valuable advice he provides at joint meetings with DB Cargo. Felix Marschner himself is also very satisfied with the cooperation: "I have a very good relationship with Mr Gimpel and the RailMaint team. We support each other, and when we arrive RailMaint staff are always on hand to help us with organisational matters and both upstream and downstream tasks, all of which we really appreciate."