Drvenjaca's 450-t press, which is over 50 years old, is now more efficient than ever with its new hydraulic system. A brilliant team effort, achieved through solutions-oriented planning and constructive cooperation.
Thanks to online shops, shopping is now very convenient and possible at any time. Your new TV, cuddly winter jacket or even hydraulic hose lines can be ordered at the click of a mouse. In order for the eagerly awaited goods to be delivered safely packaged, companies like Drvenjaca in Fuzine, Croatia, are needed. In addition to softwood chips and wood pellets, Drvenjaca also produces mechanical cellulose (RMP pulp). Drvenjača sells the cellulose internationally to companies that use it to produce multi-layer cardboard for packaging, for example.
A colossal machine
The heart of the cellulose production at Drvenjaca is the huge hydraulic press, which is over 50 years old. With a pressing force of 450 tonnes, it compacts processed wood chips into cellulose bales around the clock. The cycle for baling one of the five layers that make up a bale takes only 20 seconds. This colossal machine is therefore anything but cumbersome, even if its enormous size could suggest a certain inertia. After all, the entire plant extends over three floors: the actual press is on the ground floor, the hydraulic system is located on the first floor, and the filtration and cooling system as well as the 4,000-litre tank for the hydraulic oil are housed on the second floor. The powerful unit pumps 1,000 litres per minute through the pipes.
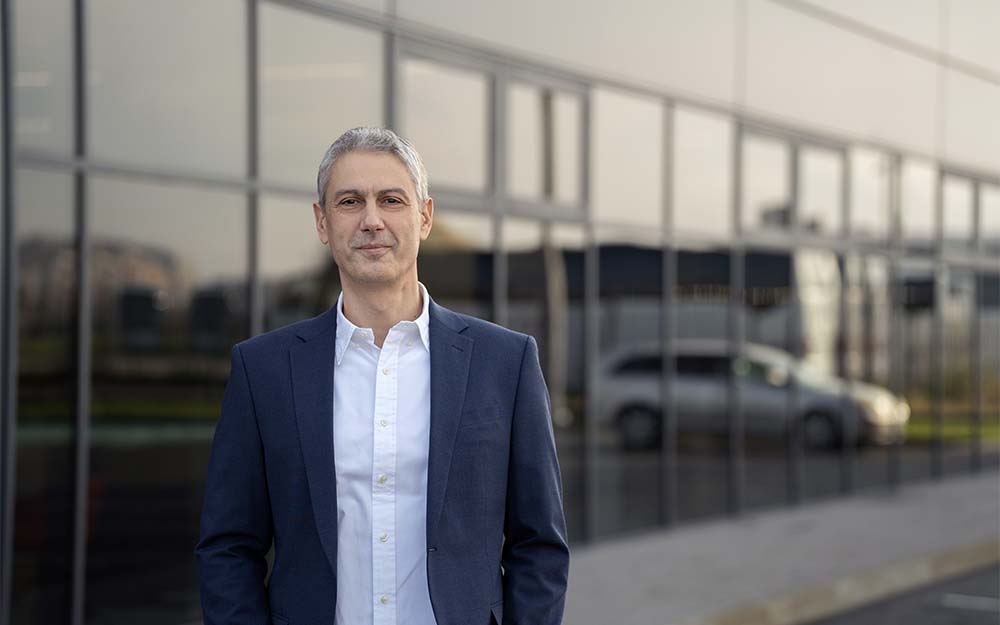
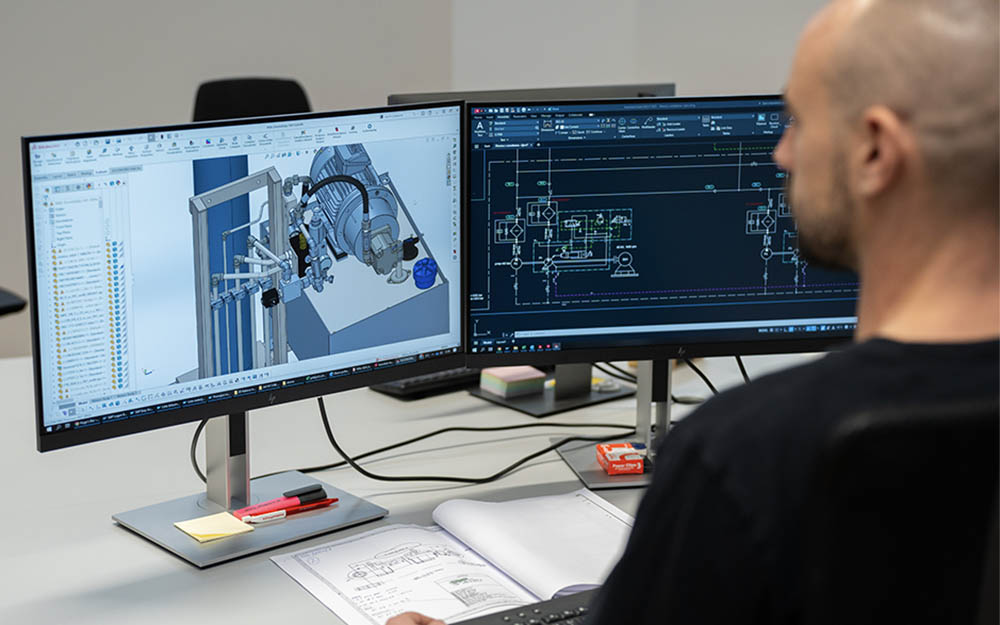
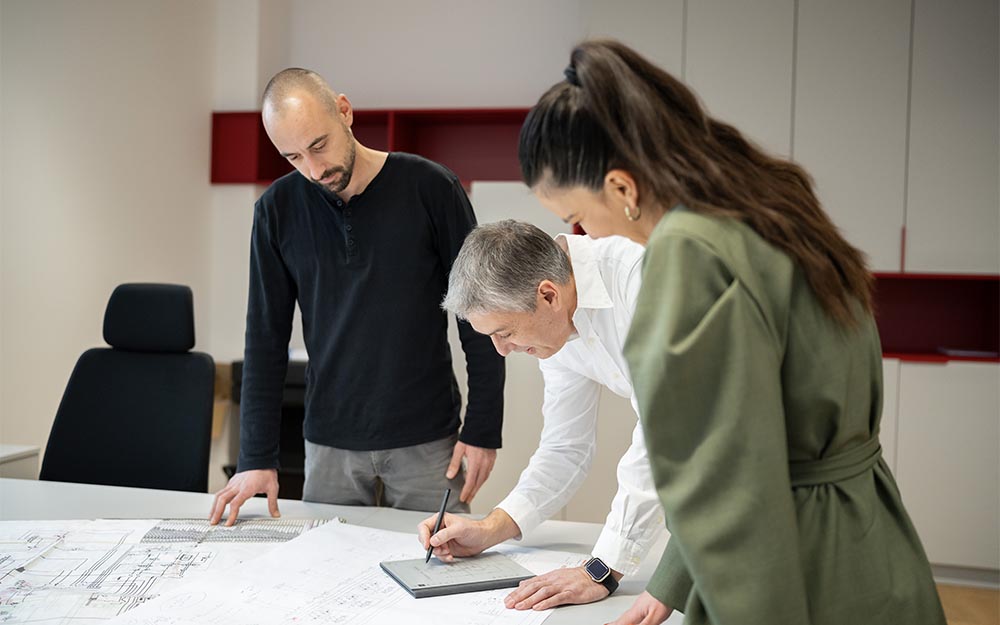
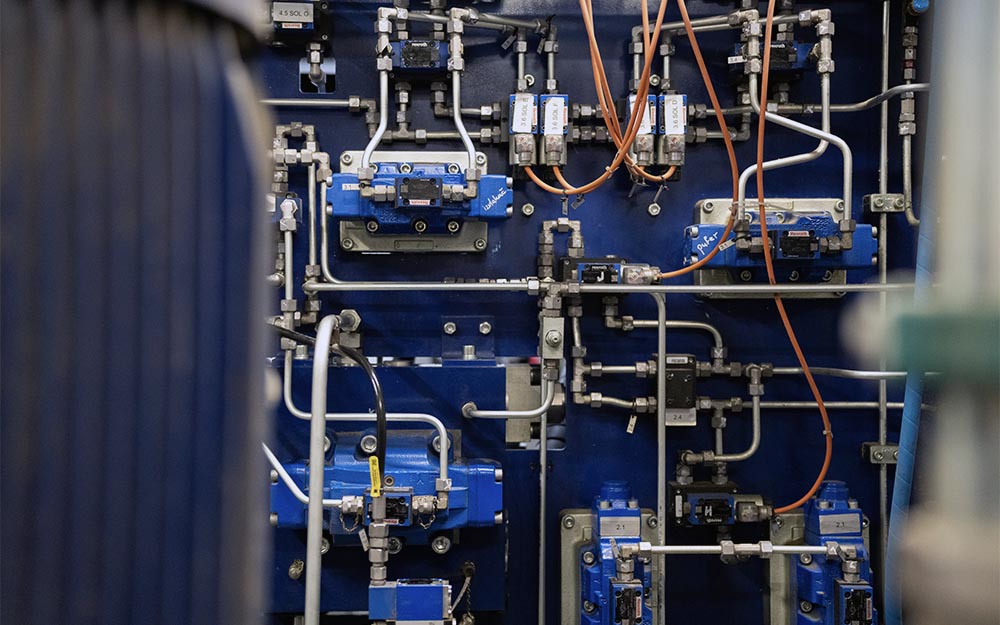
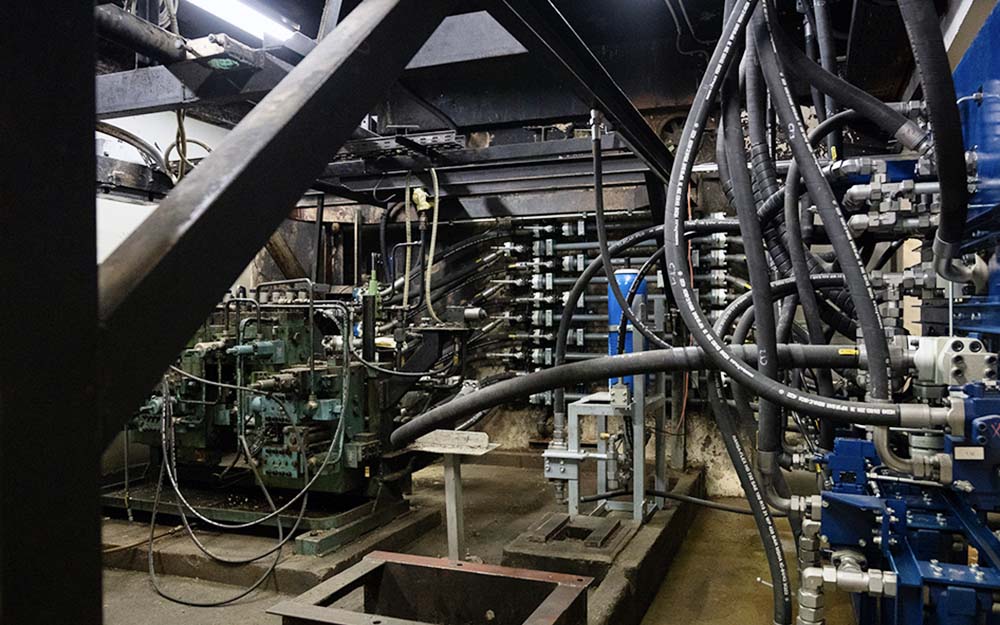
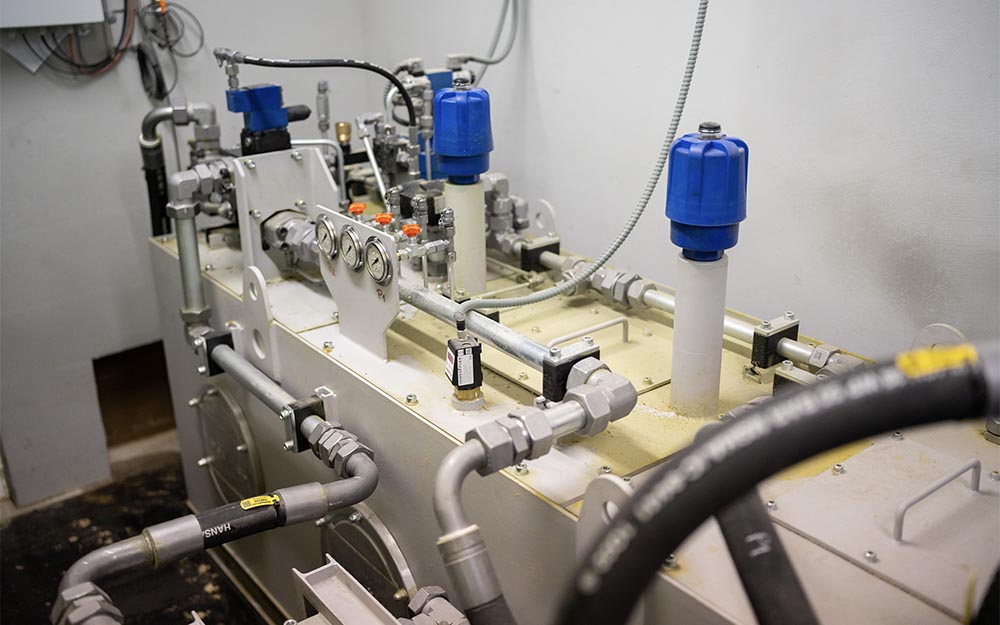
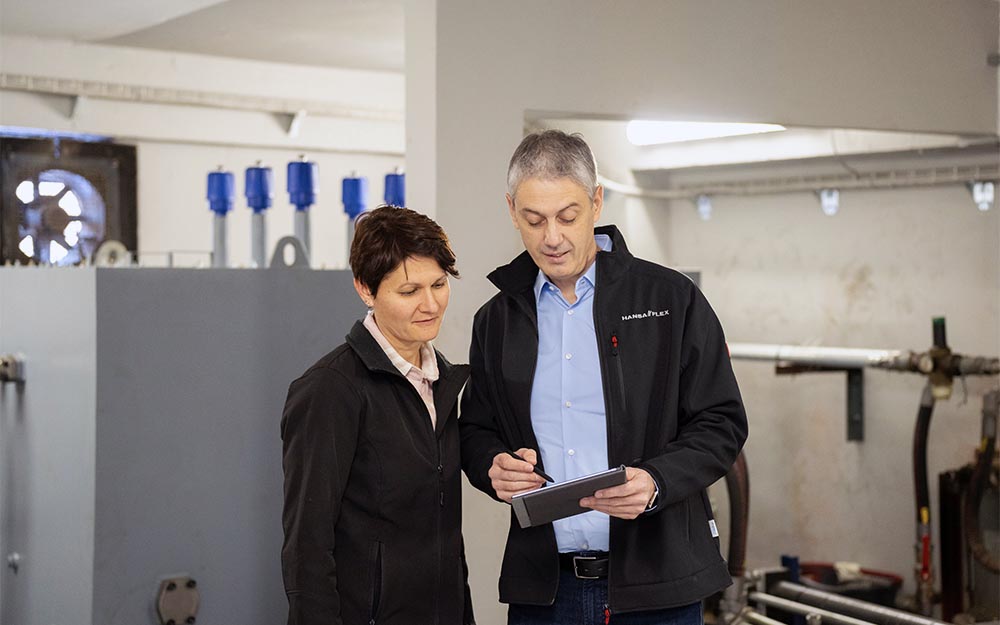
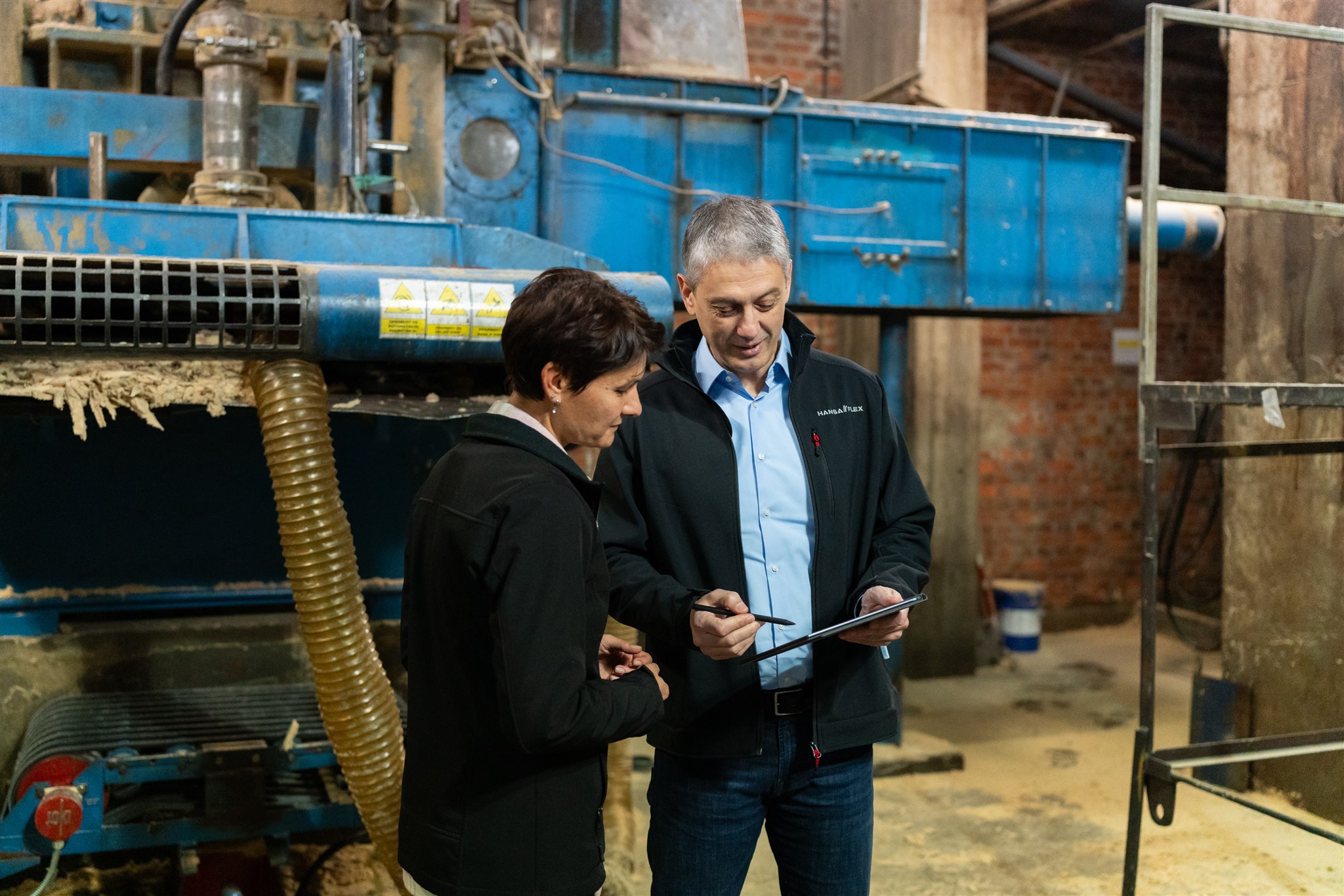
New technology for proven processes
In February 2023 Drvenjaca commissioned HANSA‑FLEX to modernise the hydraulic system. "The main idea behind this programme was to modernise the hydraulic system of this press by installing standard components in the hydraulic drive. The old system was custom-made, so the components were expensive and difficult to source," explains Ana Starcevic Radosevic, Investment Manager, Drvenjača d.d. In order to design a modern twin that can identically map all the processes of the hydraulic press with standard components, the HANSA‑FLEX engineering team led by Petar Curac, Technical Manager, HANSA‑FLEX Croatia, first created a 3D model of the existing system. A team of five engineers put a significant amount of work into modernising the press, including analysing the old system, participating in the development of the new solution, creating the new 3D model, preparing the documentation, and testing and commissioning the new system. "It's a bit like putting together a good orchestra, no instrument can be missing, everyone has to be in the right place," says Petar Curac. With more than 200 kW of engine power, the development and installation of the new hydraulic system for Drvenjaca was the most complex and time-consuming project for HANSA‑FLEX Croatia to date. The work was completed in just under nine months. Ana Starcevic Radosevic is positive about the successful cooperation: "I am very satisfied with the results of the project. We have a new drive system that consists of lightweight standard components and the HANSA‑FLEX team is always very cooperative, whether we need the advice of the engineers or quick action by the technicians!"
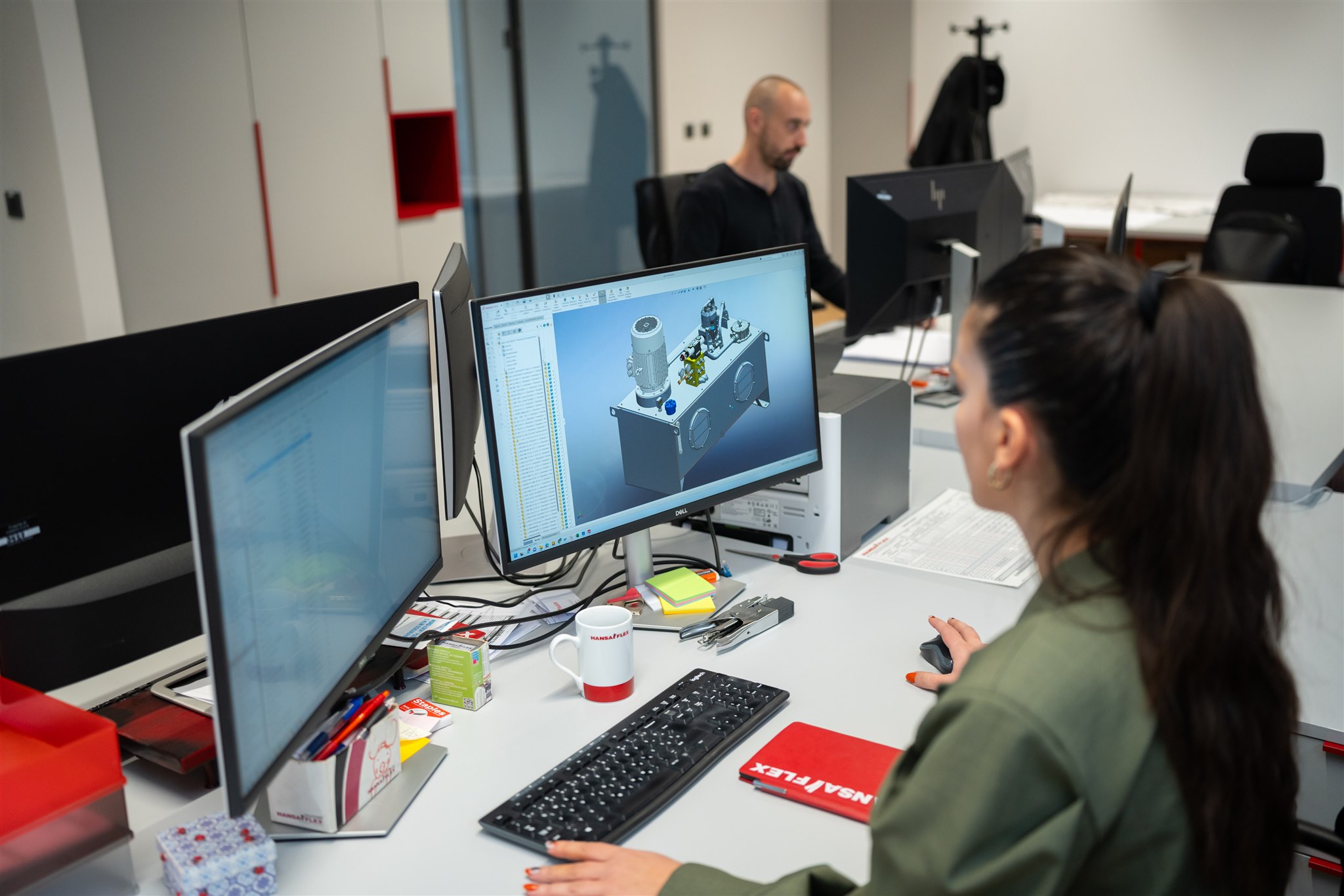
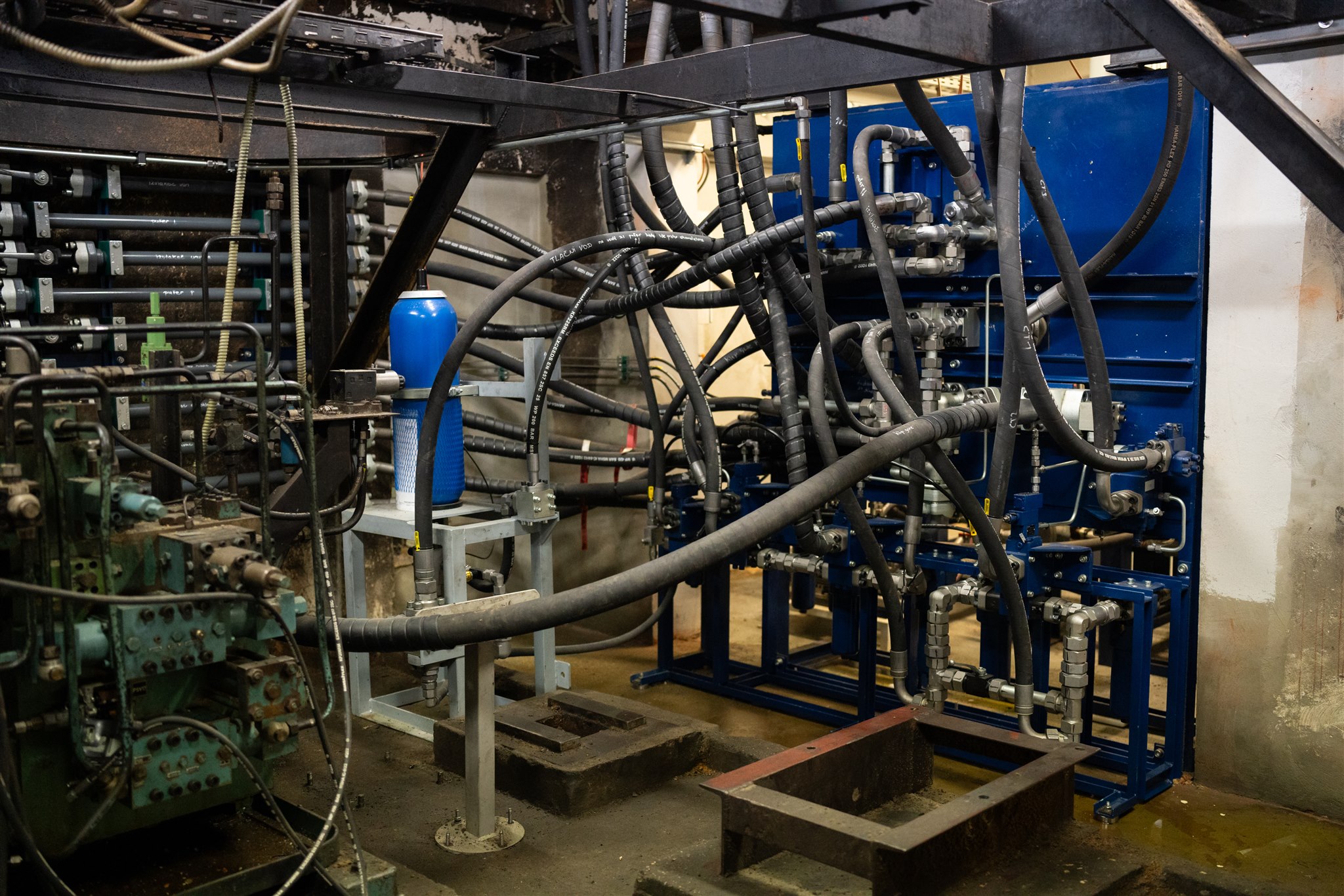
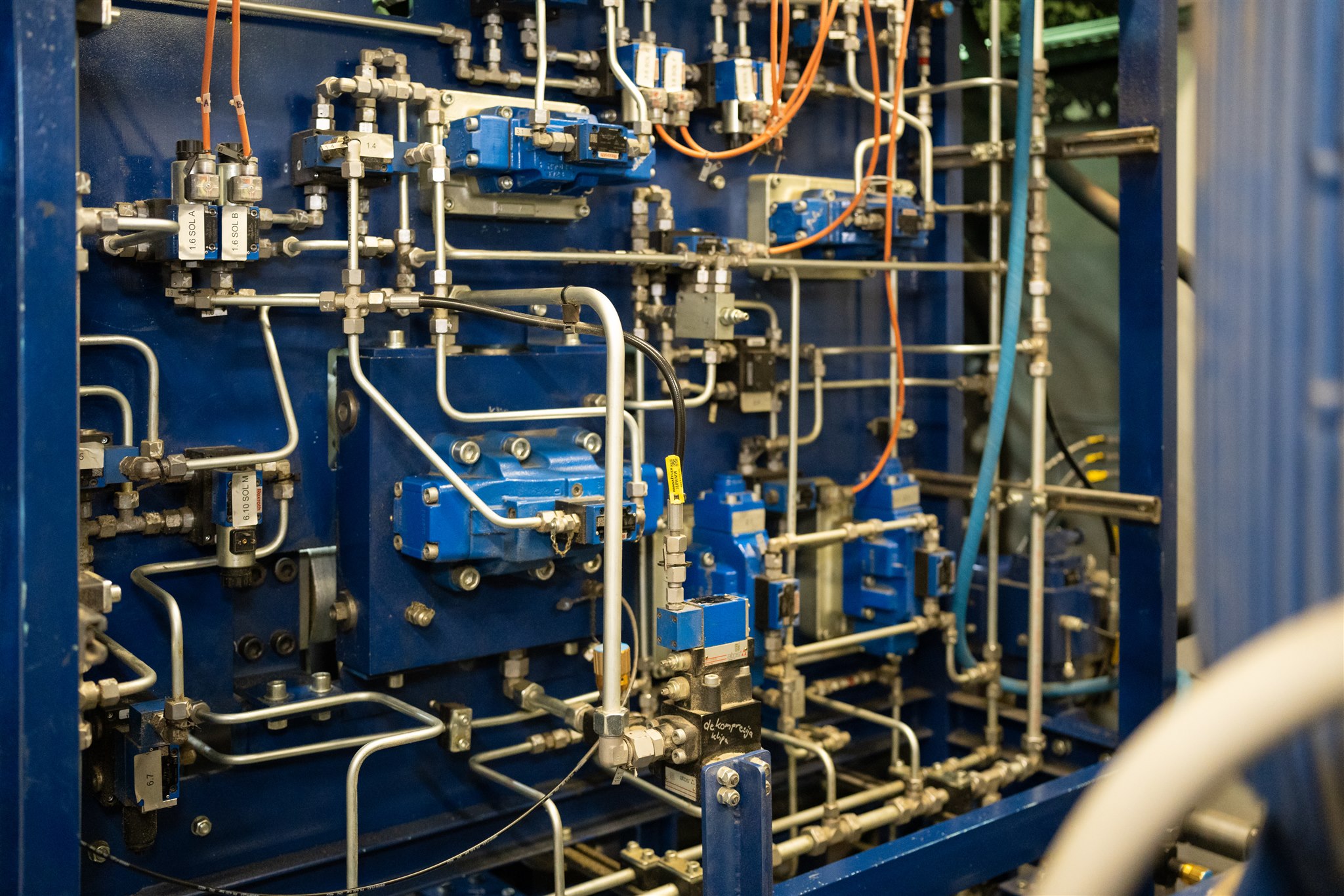
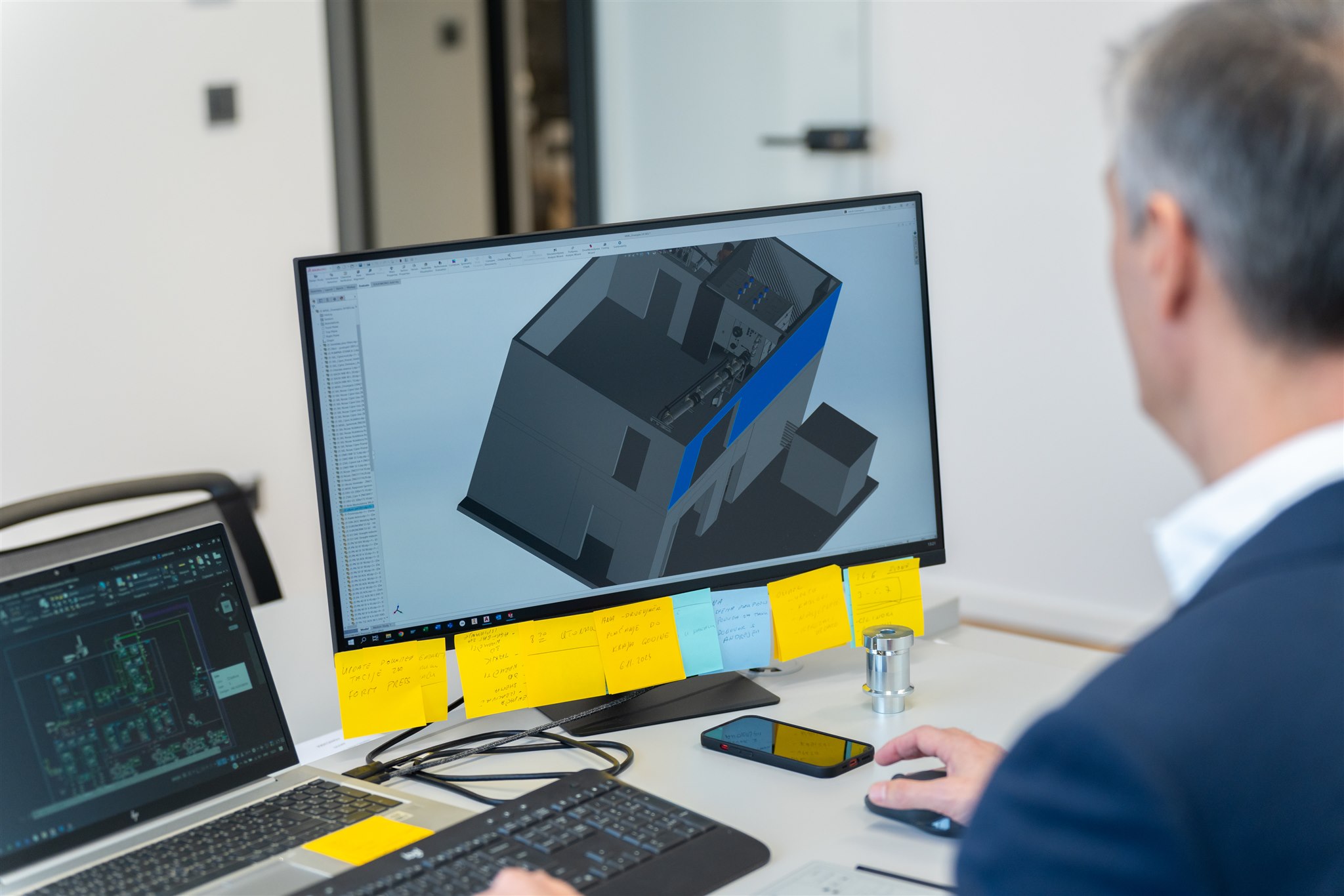
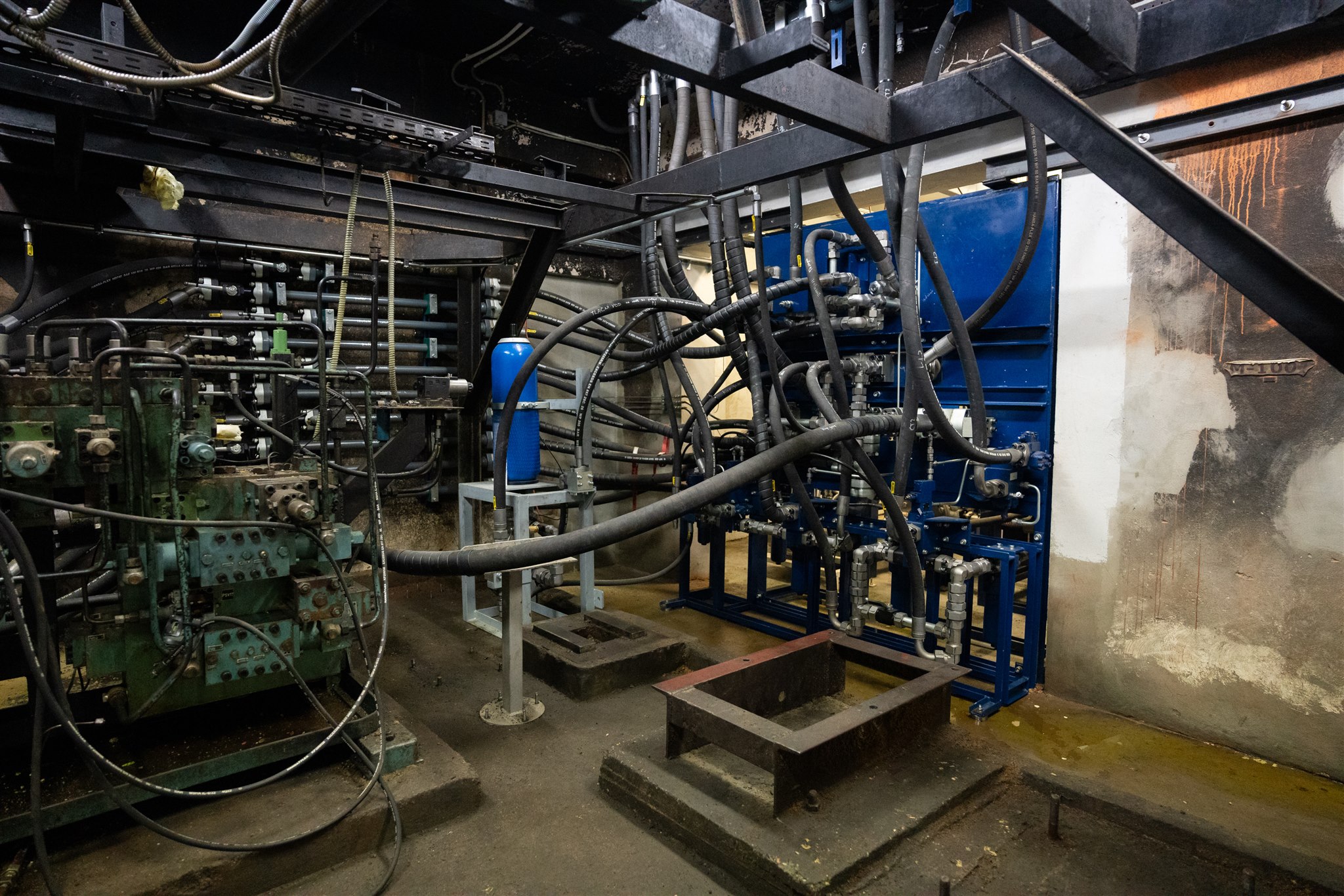
An enormous increase in efficiency
Drvenjača worked closely with the Hansa-Flex team to make the switch to a new drive system a reality, while retaining all the features and capabilities that the machine had with the old system. The biggest challenge was to determine the exact parameters that Drvenjača had for each action on the press, and to design the new system accordingly. The initial plan was to operate the new hydraulic system in parallel with the old one. At the end of the day, however, the new system designed by HANSA‑FLEX turned out to be much more efficient, which is why it has completely replaced the old system. "By using special valves, for example, we were able to reduce the operating pressure from 280 to 220 bar. This significantly increases the service life of the system without sacrificing productivity, and also results in energy savings," explains Curac. If the hydraulic press should fail, it would take a long time to restart production due to the large number of parameters involved. For this reason, predictive maintenance measures such as filter replacement and oil analysis are important service components that HANSA‑FLEX as a service partner continues to provide for Drvenjača with the help of the X-CODE Manager. A new press is also already being planned together – this time with a massive 1,000 tons of pressing force.