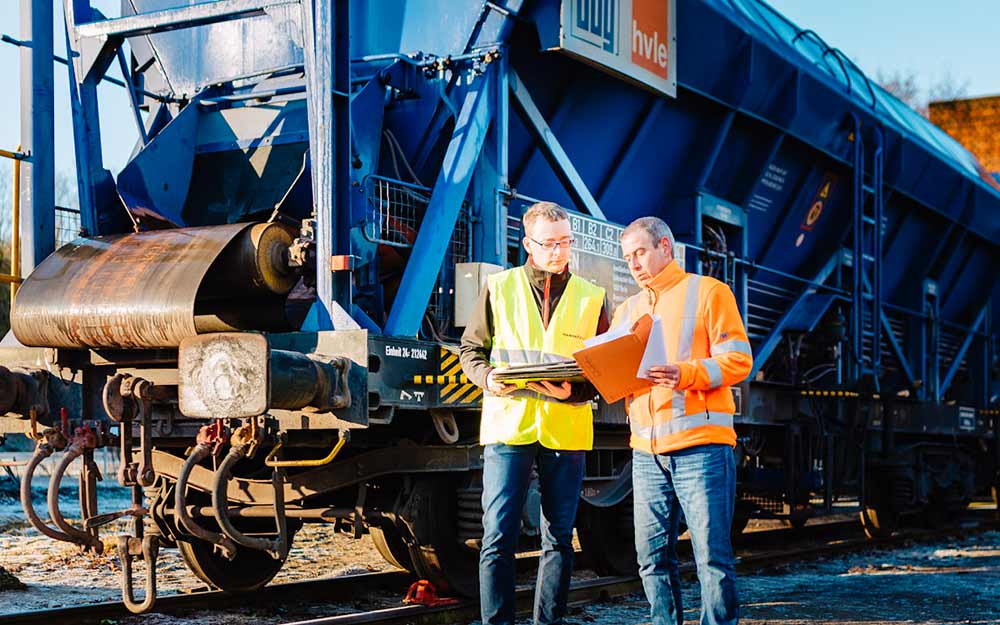
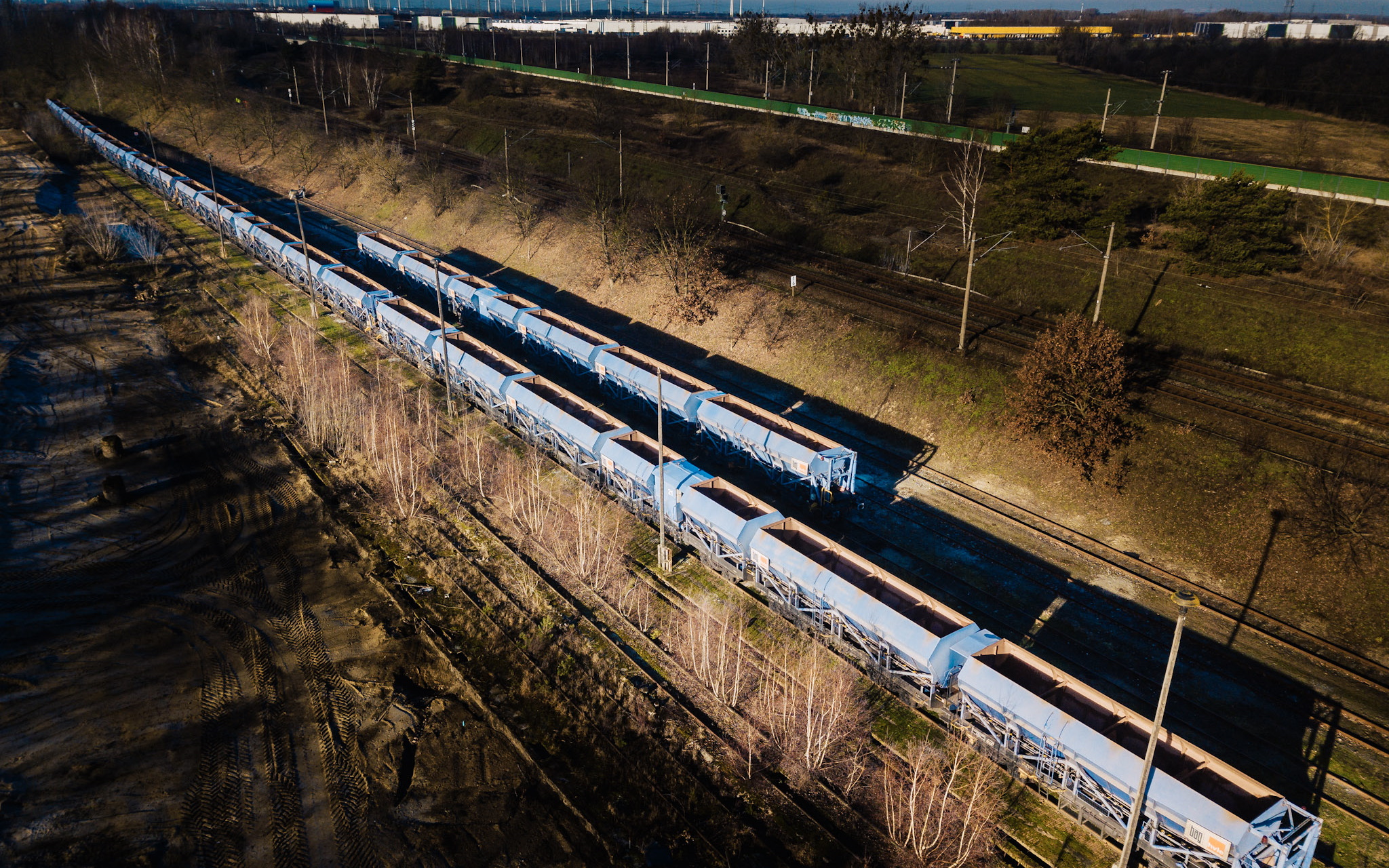
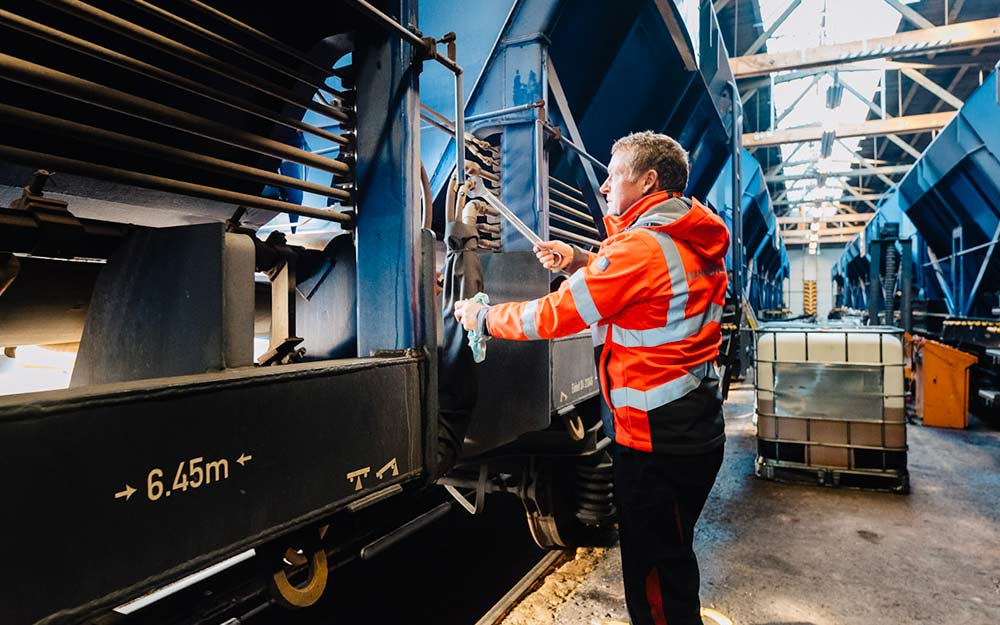
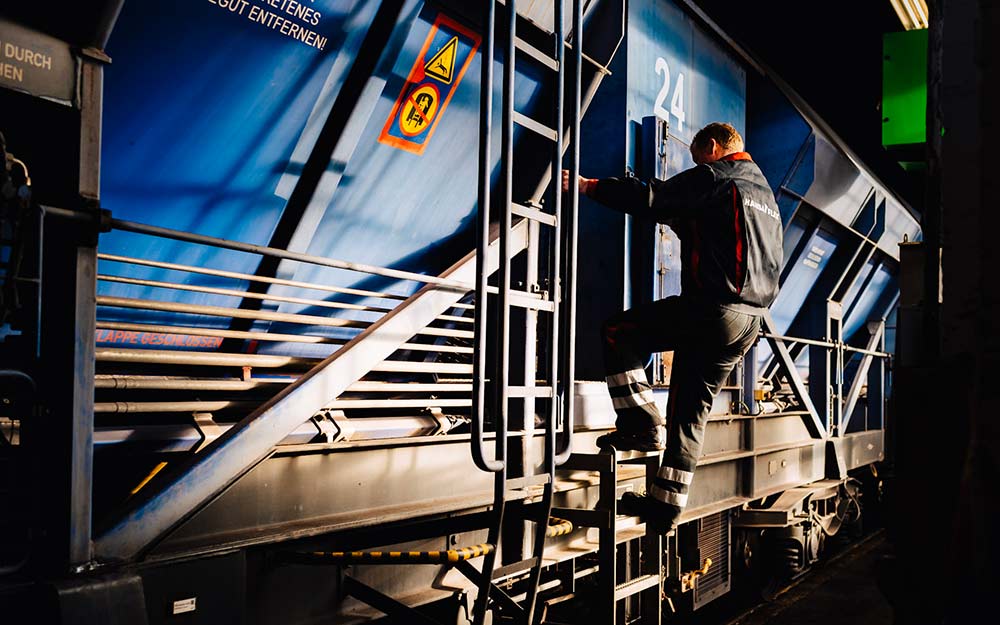
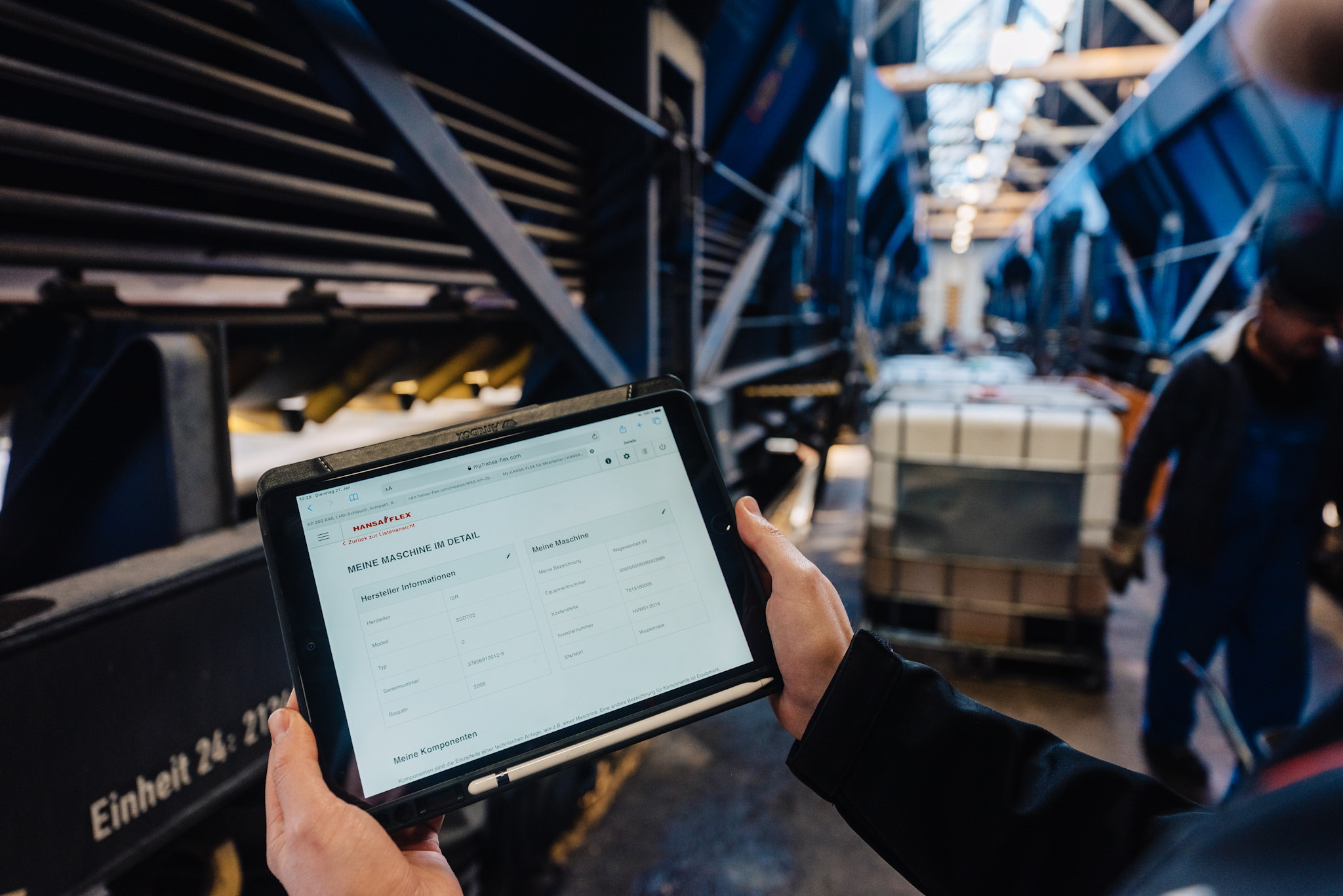
Unloading by conveyor belt
In order to start the discharging process, the three members of the HVLE unloading team close the gaps between the units by folding down conveyor belt bridges. This is carried out to a large extent automatically by remote control. Once the sections are closed the conveyor belts go into operation. When a hopper is opened, its cargo trickles through a hatch onto the belt and is transported to the middle of the train. This is where the discharge wagon is located. Its telescopic boom can be swivelled by 120 degrees and bridges the last metres to the destination with a conveyor belt. Around 750 t per hour can be discharged in this way - completely without any external power supply, as each unit has its own diesel generator for the hydraulic system. In order to serve another unloading location with a different type of bulk material, it is only necessary to move the discharge wagon a few metres further and open another hopper.
Mobile service around the clock
Diagnosis by the Fluidservice
The empty train now begins its journey back to Saxony-Anhalt. There it is loaded once more and a new 24-hour shift begins.