From granulate to mould
Christmas peak time
Other sections help
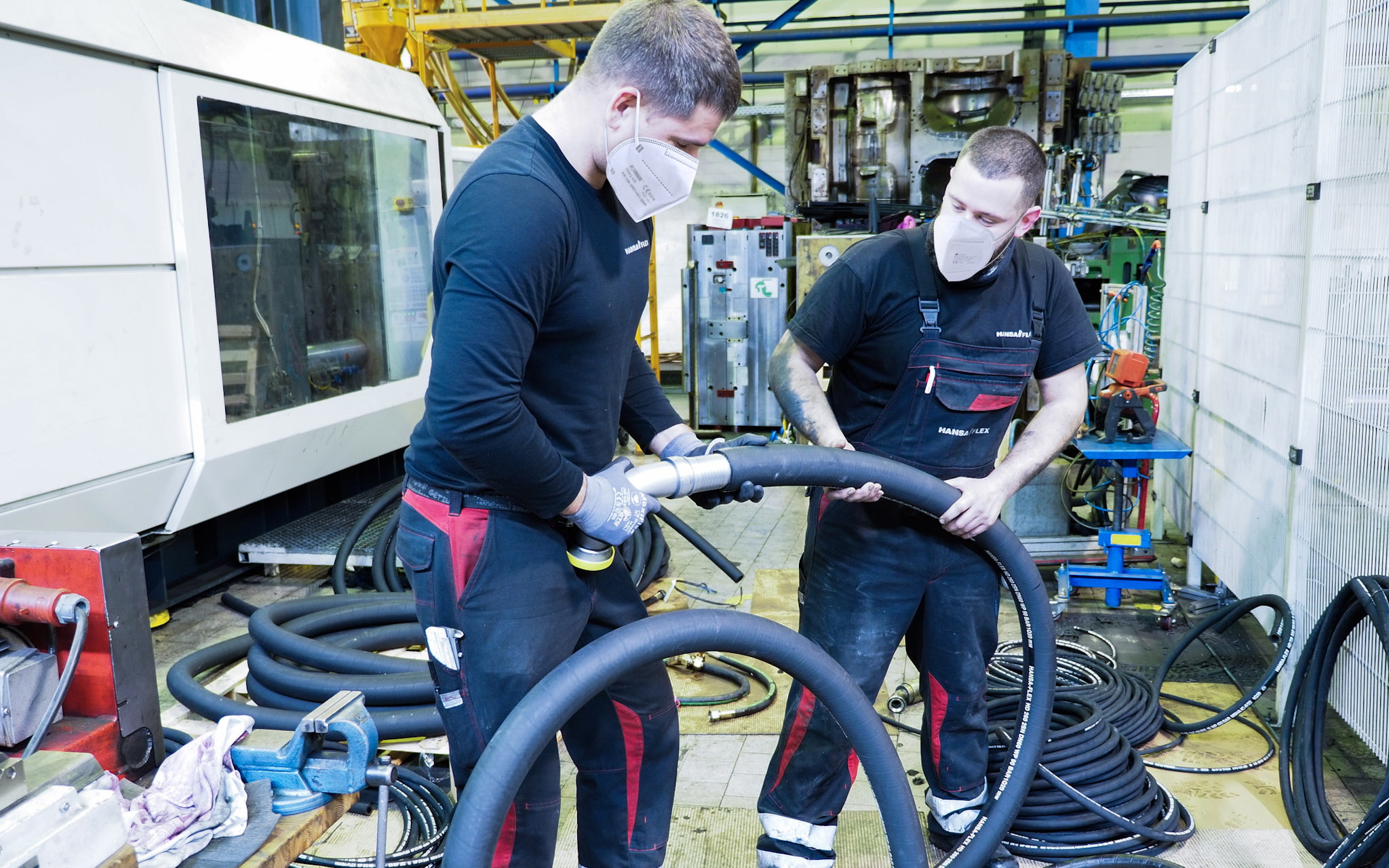
Do you have any questions about our services and products? Or do you need help?
Sundays and public holidays are excluded
KKF Fels GmbH commissioned HANSA-FLEX to change the hose on an injection moulding machine
With the modernisation of a 450-tonne press, HANSA-FLEX Croatia has successfully implemented its most complex project to date.
When most people come to rest at Christmas, things get busy at KKF Fels GmbH. That's when the automotive supplier's injection moulding machines run around the clock. Since the end of 2020, HANSA-FLEX has also been getting involved.
The hoover factory of BSH Hausgeräte GmbH and the HANSA-FLEX branch there are located next door to each other in Bad Neustadt.