A longstanding partnership
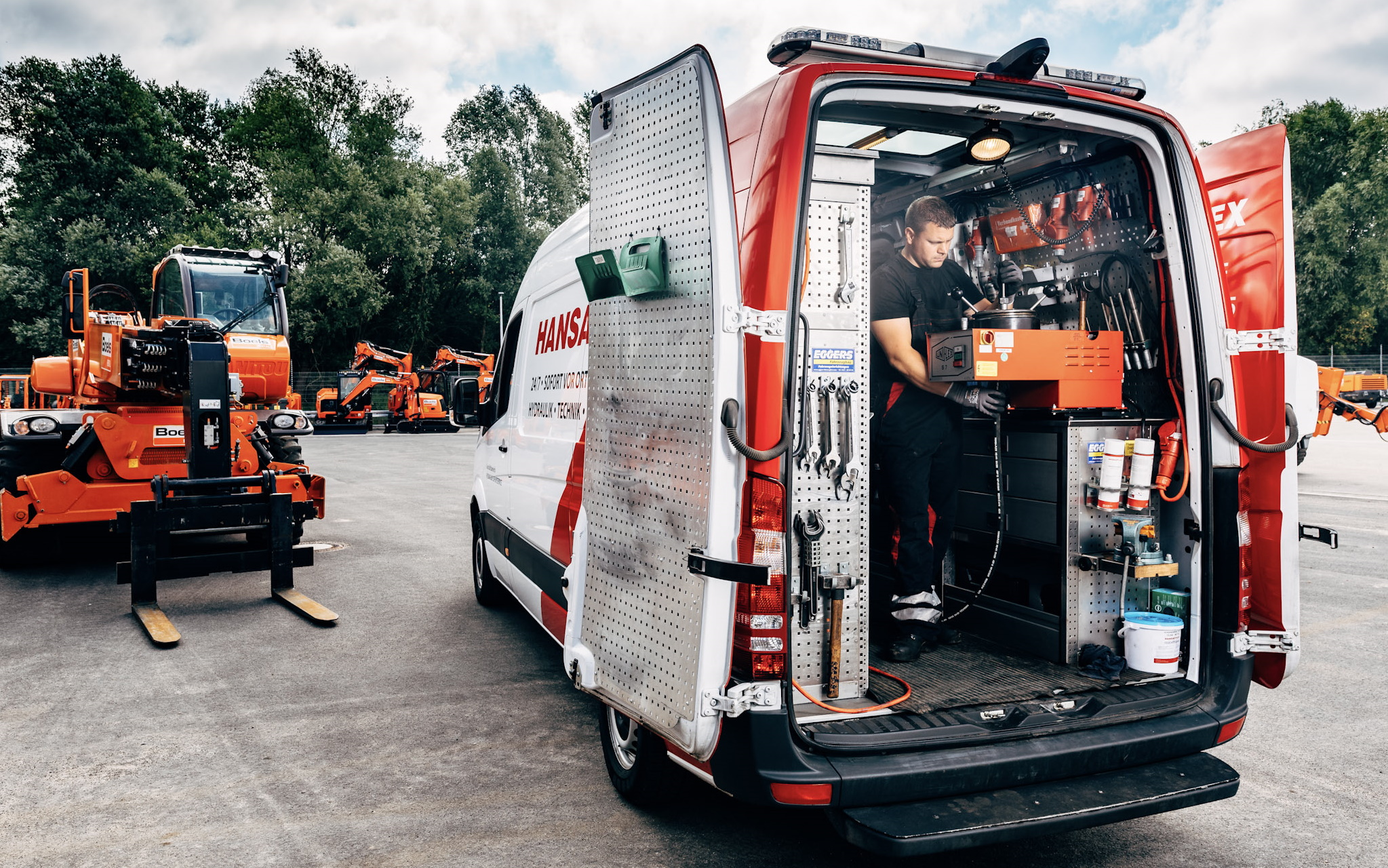
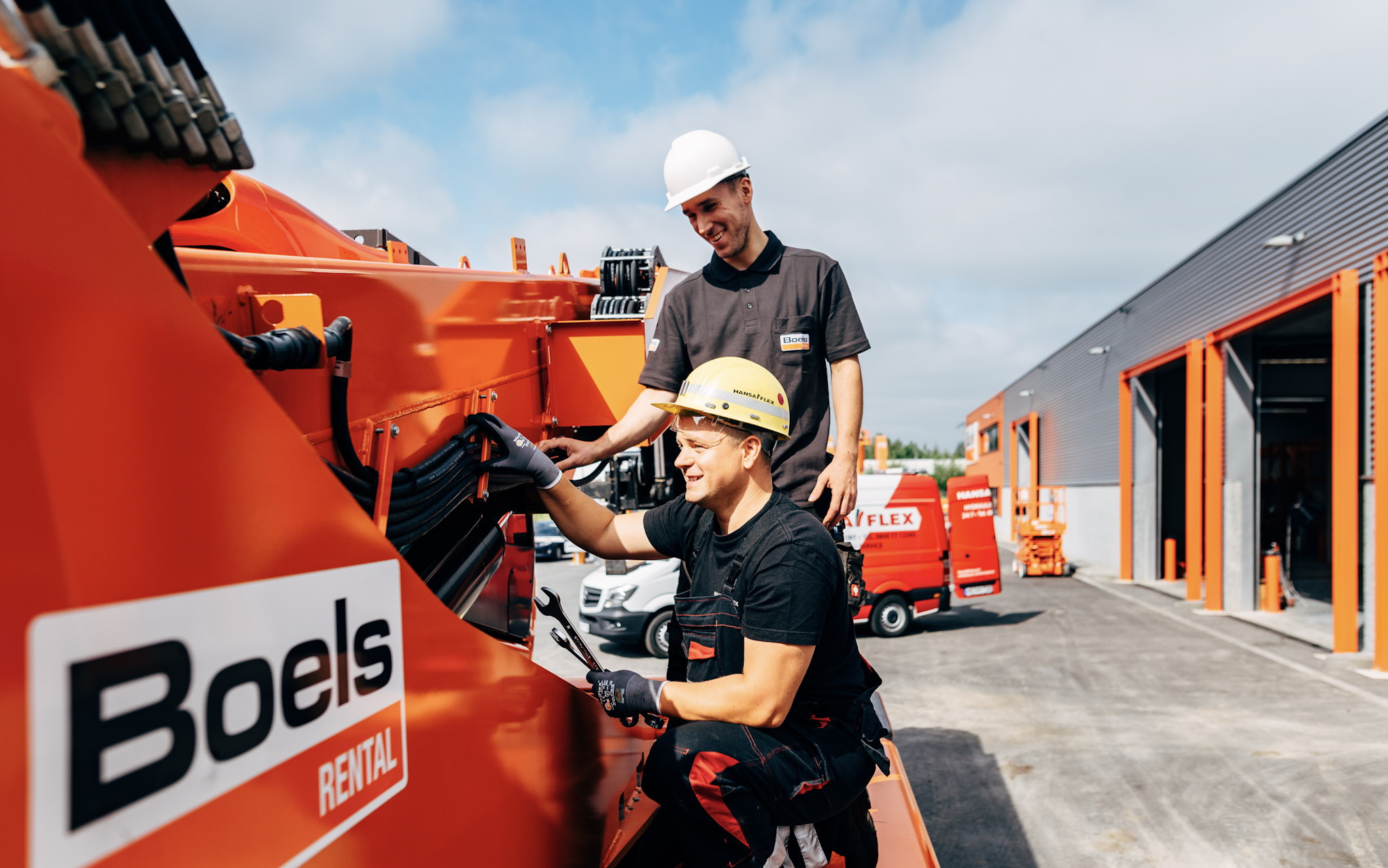
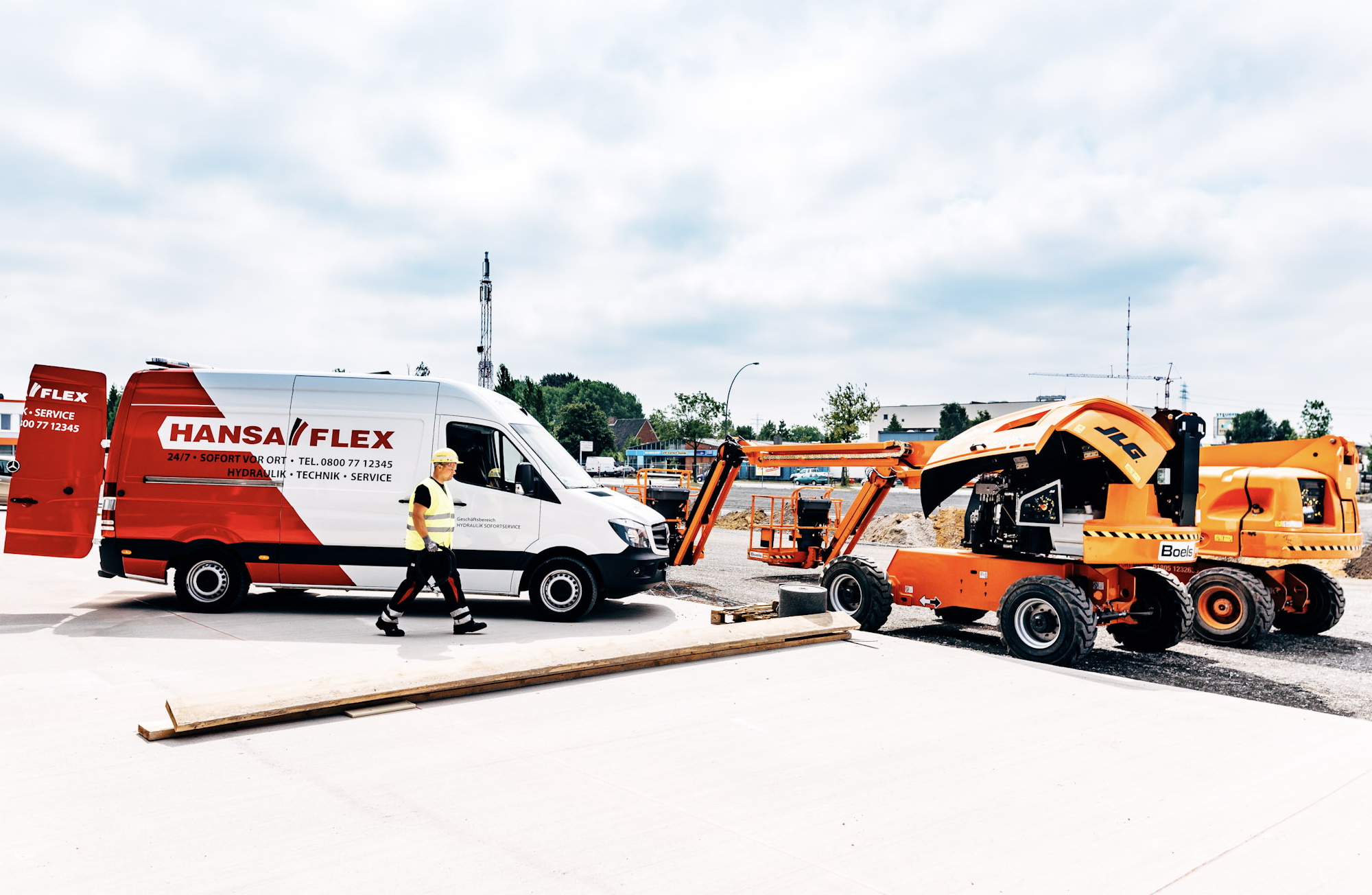
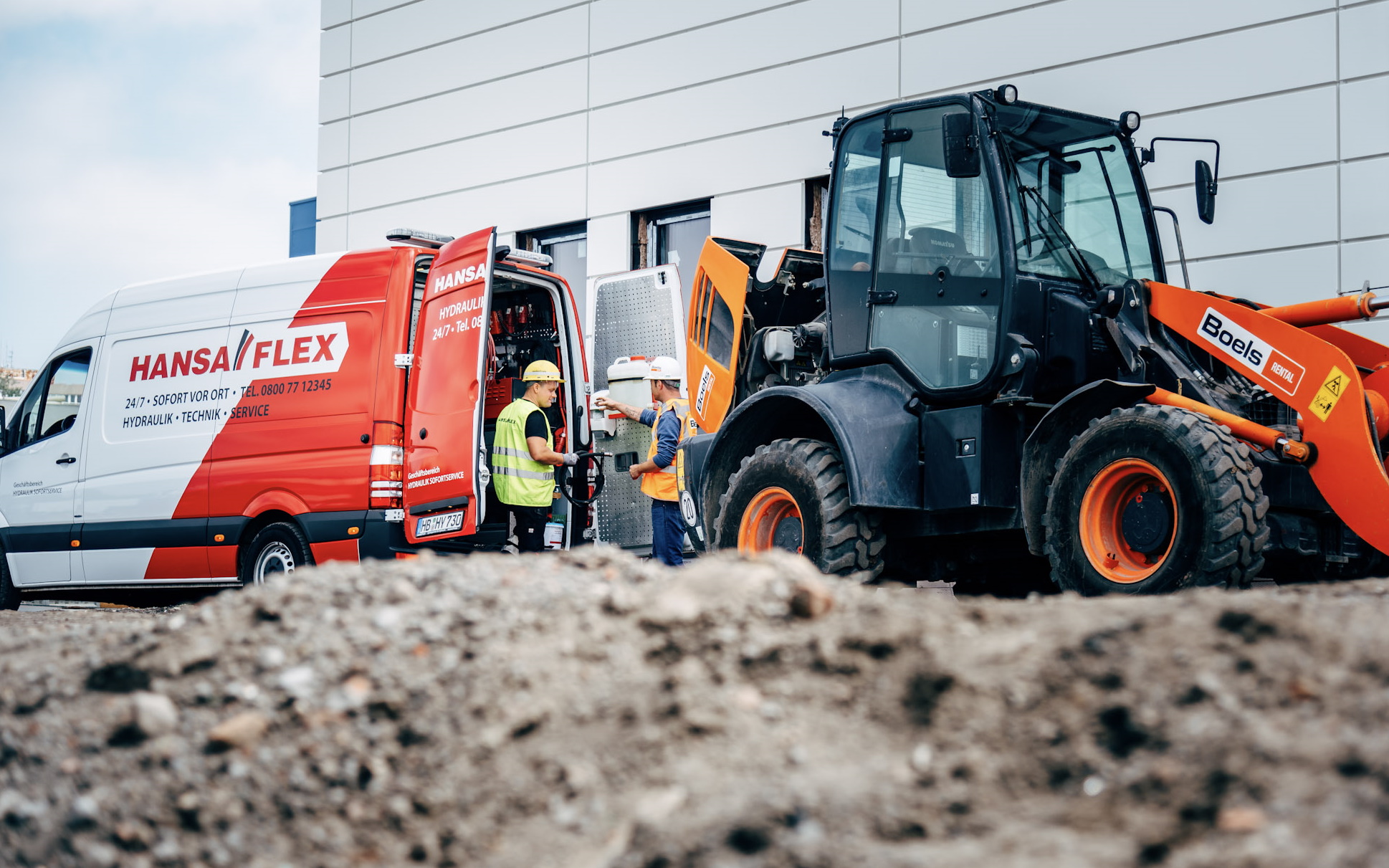
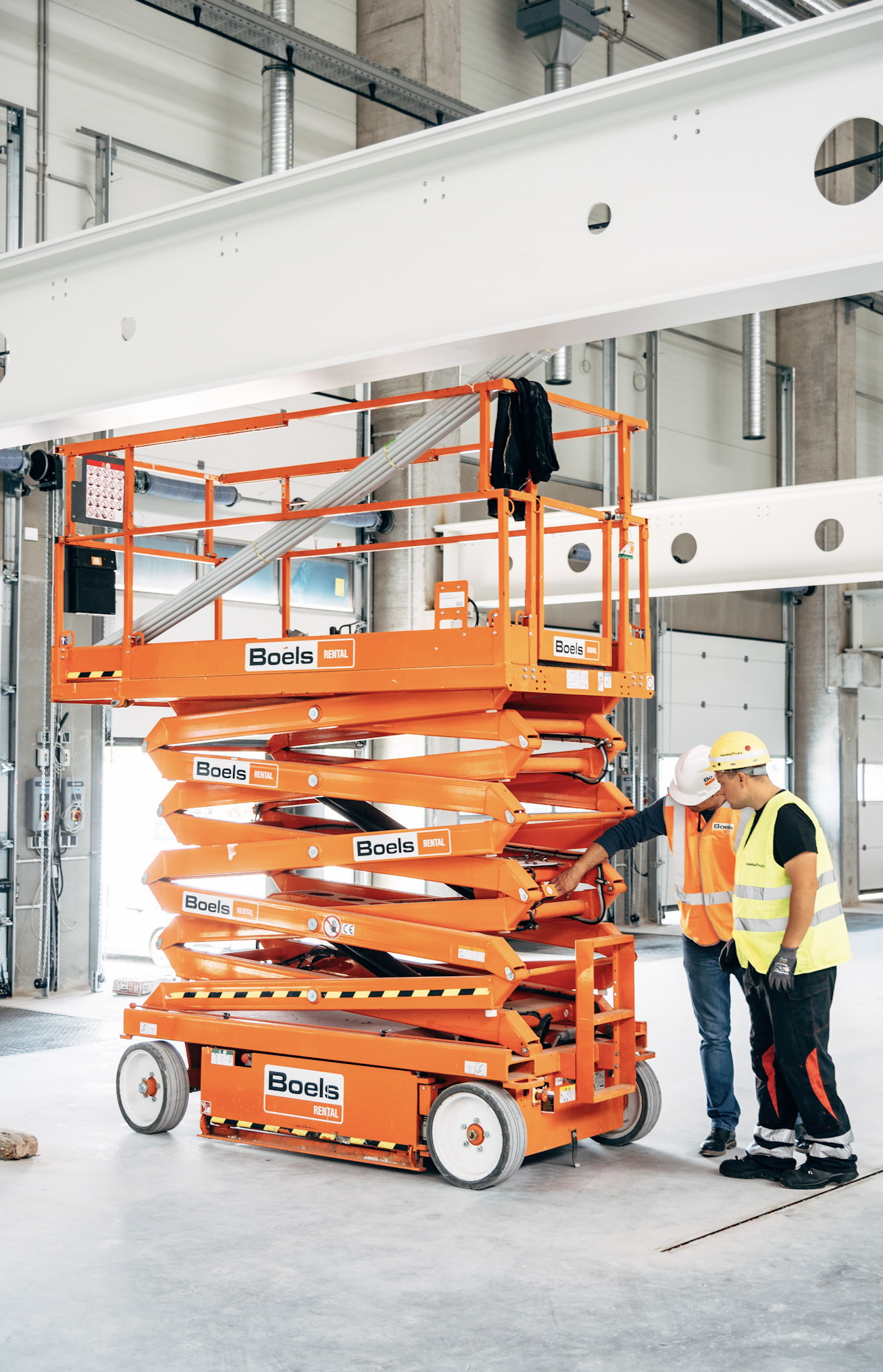
Do you have any questions about our services and products? Or do you need help?
Sundays and public holidays are excluded
Boels Rental relies on the fast reactions of the Rapid Hydraulic Service
A building site surrounded by water? terra infrastructure makes it possible, while HANSA-FLEX provides the heavy-duty hydraulics required.
Individual requirements, standardised solutions: at the customer's request Kiesel equips excavators with a wide variety of attachments and conversions. Hose line kits from HANSA-FLEX play an important part in this.
The HANSA-FLEX Fluid Service in operation at Holcim: how clean oil contributes to sustainable cement production.