This often involves quickly switching between products at the factory, something that is of course only possible with sophisticated process technology and high logistical efficiency. Tankers containing fresh milk for the dairy products constantly roll up at Gütersloh. Other deliveries include ingredients such as fruit pulp, processed fruit, chocolate chips, cream or sweet woodruff, as well as containers of all shapes and sizes, already equipped with labels for the different brands. There are of course also boxes, which are then put together as crates on pallets for shipment. Every day between 1,200 and 1,500 pallets leave the factory laden with their delicious cargo, ready for distribution throughout Europe.
Blended in the container
Line engineering plays a key role at the company. Things are of course rather tight at the filling machines. To fill a crate with twelve 500 gr containers for example, the feed lines for the ingredients have to be connected to the relevant filling heads. Special pipes were once used for this purpose. This resulted in awkward situations as they sometimes had to be bent into complicated shapes to fit into the confined space available. Great accuracy was required to compensate for the slight deformation involved. Fast and flexible changeover of the production machinery was difficult due to the time-consuming process necessary here.
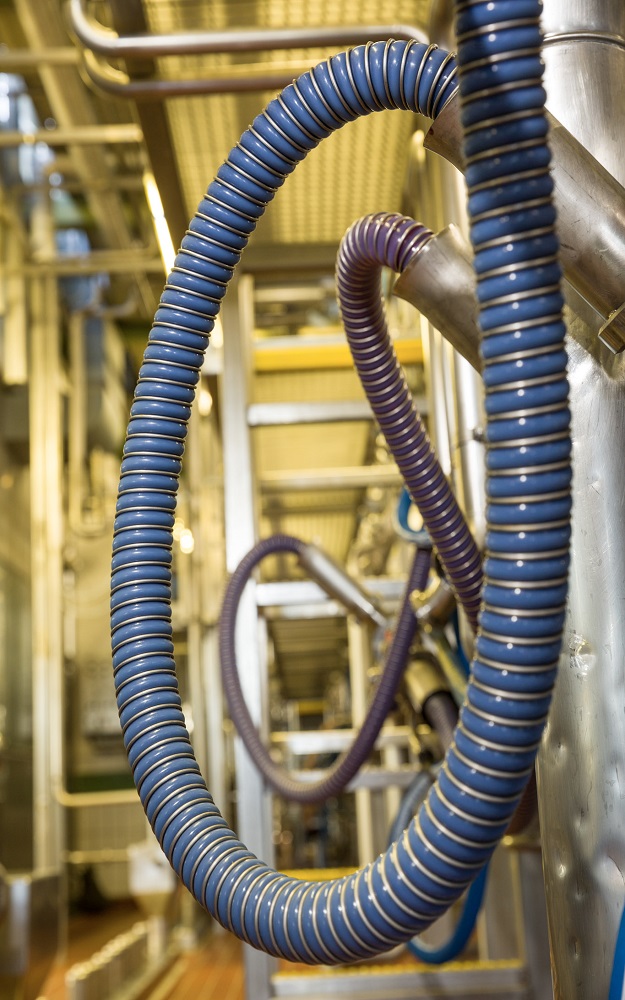
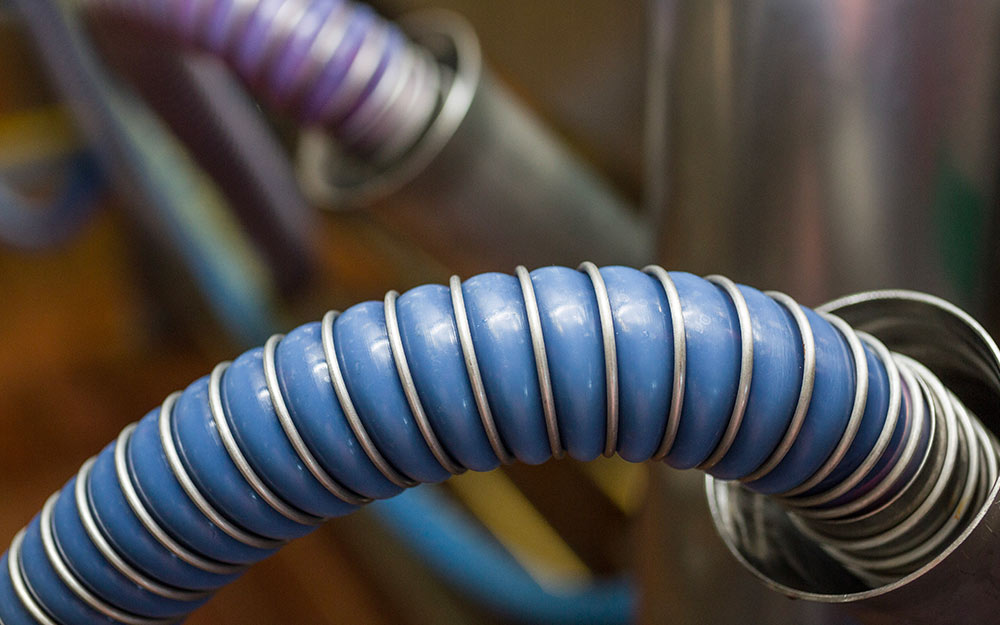
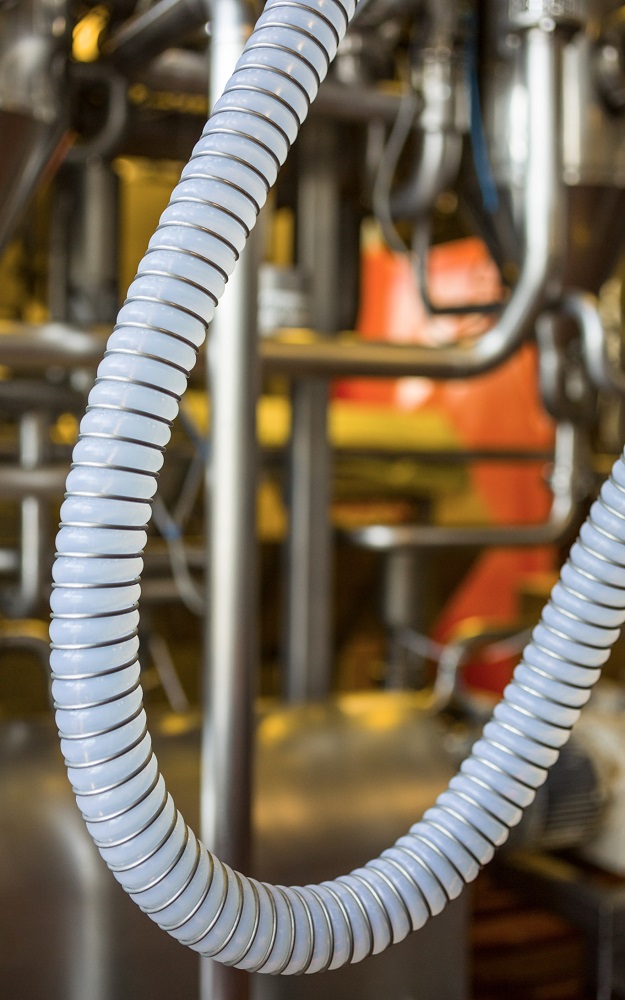
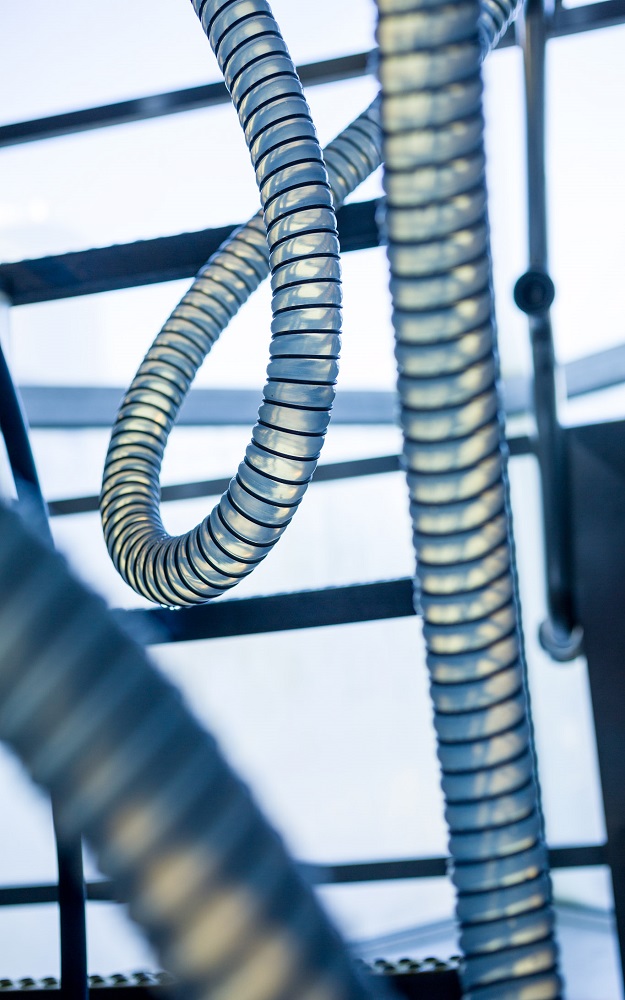
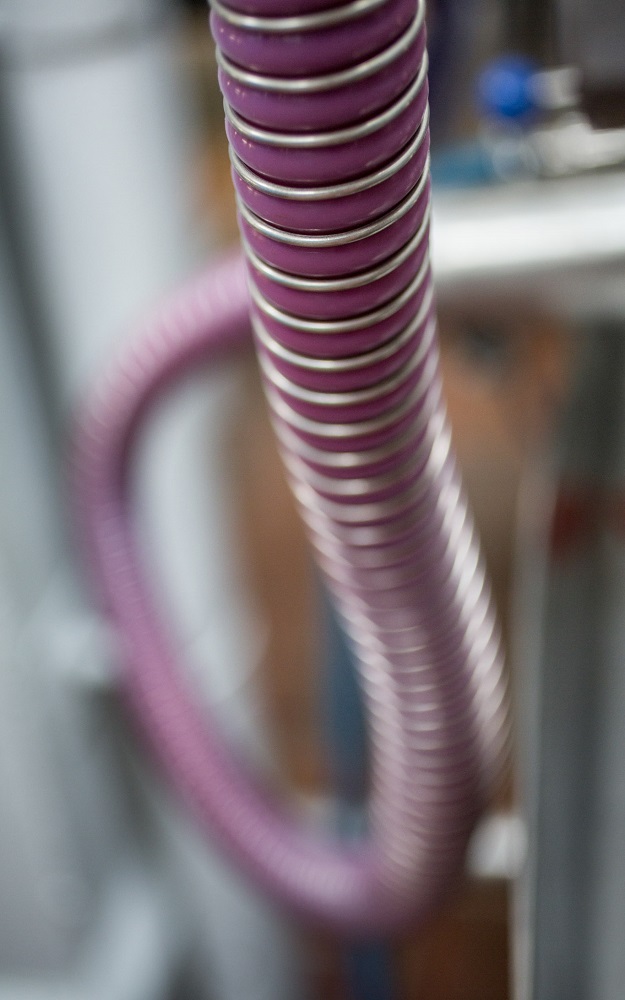
The solution: PTFE
“But HANSA‑FLEX proved to be very patient and always responded quickly,” said Mehmet Susever, who is still delighted about their cooperation. “And even at the weekend we didn’t hesitate to commission HANSA‑FLEX with the production of hoses. As the plant works non-stop, this meant we had to make use of the tight time slots available when the machines were being cleaned and prepared for new campaigns.” The specialists in Boffzen have proved themselves to be committed partners to Campina, something that has remained unchanged today. “HANSA‑FLEX is always at the end of the supply chain in terms of process technology - in other words, we can only determine the exact measurements for the PTFE hoses once a process line has been converted,” remarked Mehmet Susever. “But very fast delivery is then required. We order the hoses by phone, and they’re available just a few hours later.”
One special advantage of PTFE hoses is of course their flexibility, which caters for minor variations in dimensions. They offer the necessary flexibility so that at filling plants, the feed lines can be quickly connected to the filling heads. Campina can thus achieve a significant reduction in set-up times and process costs.
At a plant that continuously manufactures fresh dairy products unscheduled downtimes should never last very long. This is why Rainer Kahmann, as the manager of the technical warehouse, has localised all key spare parts and keeps sufficient stocks of these components. Including of course a small supply of PTFE hose lines, articles which really only become unusable due to improper handling or mechanical influences. To avoid such influences Campina also uses PTFE hoses in areas where filling does not take place. These hoses feature a metal braid jacket or are protected from abrasion through contact with the ground by double metal spirals.