
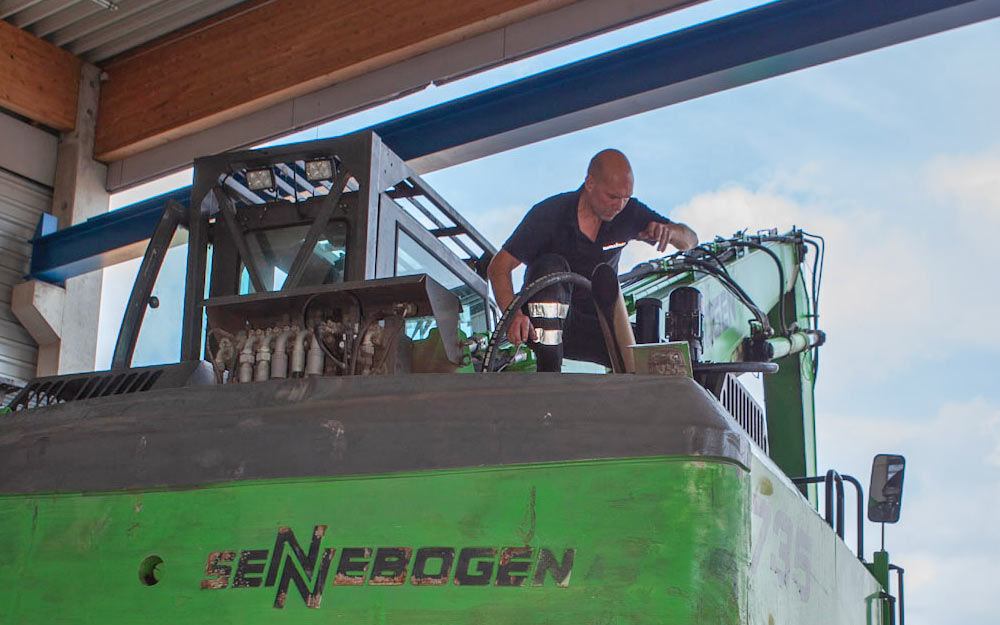
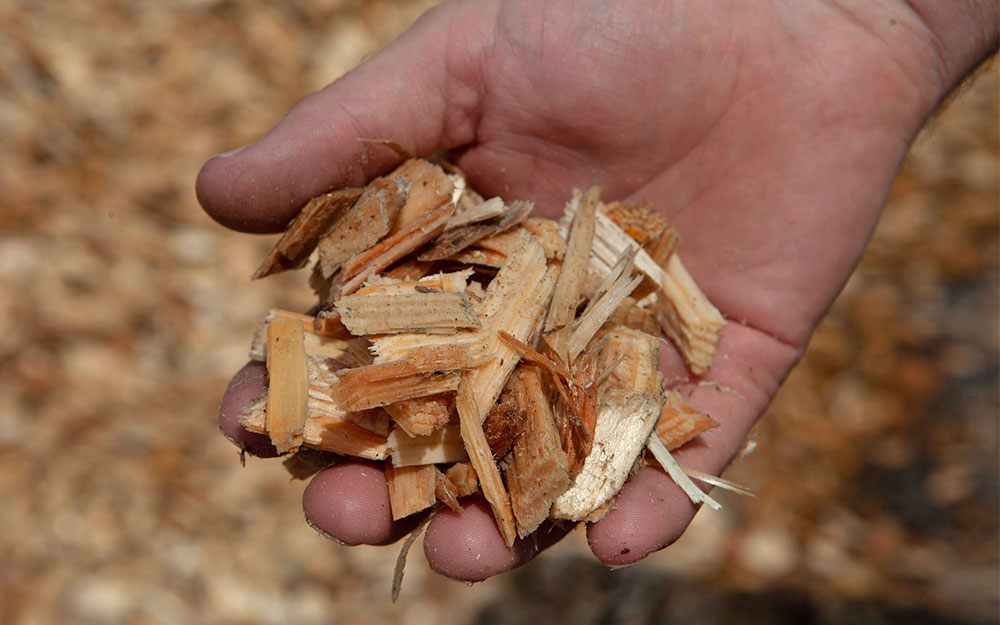
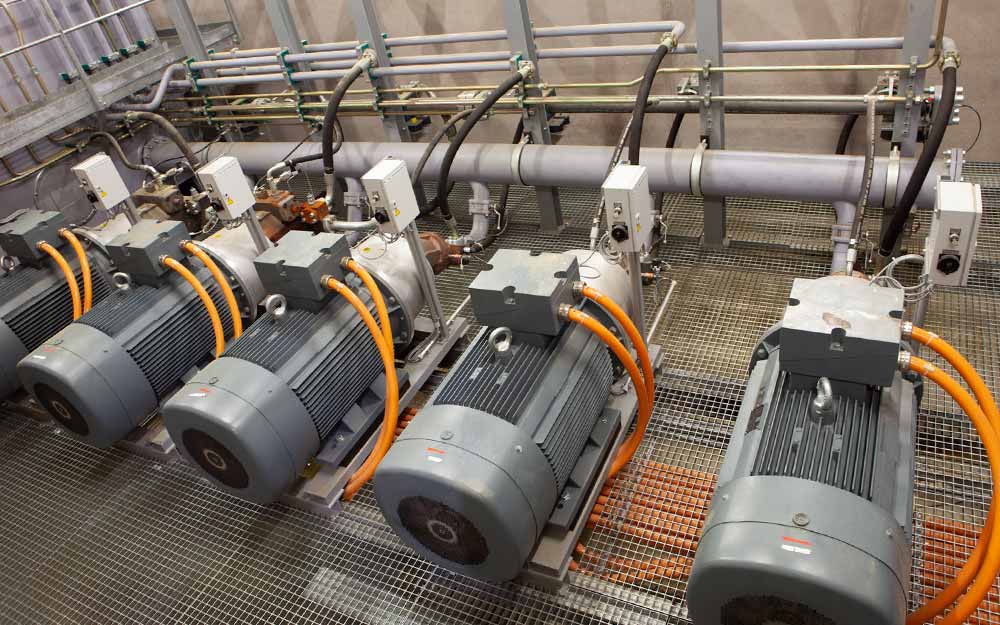
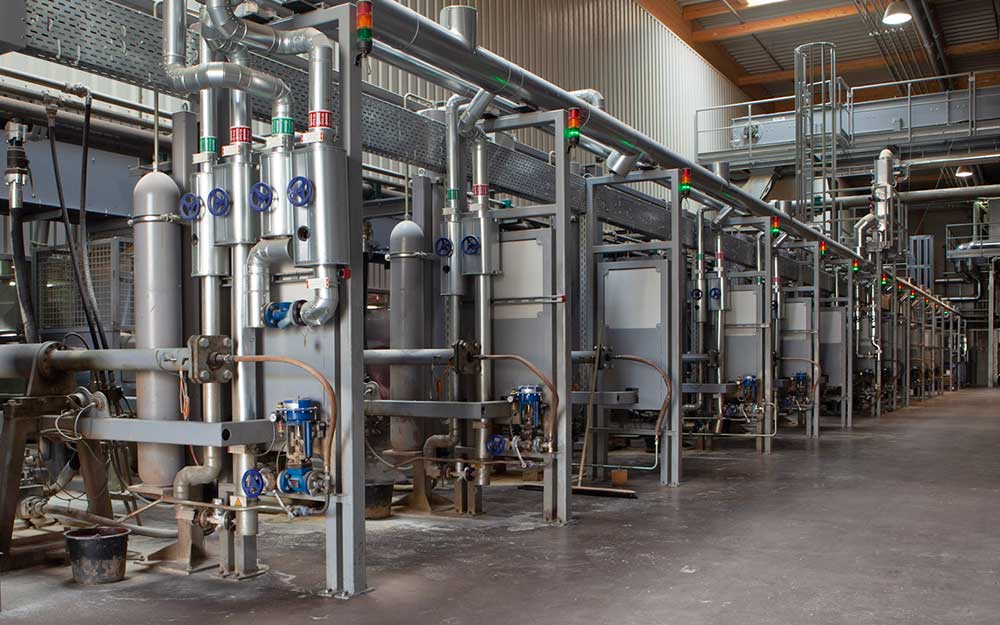
From logs to lumber
Imposing figures
The full spectrum of hydraulics
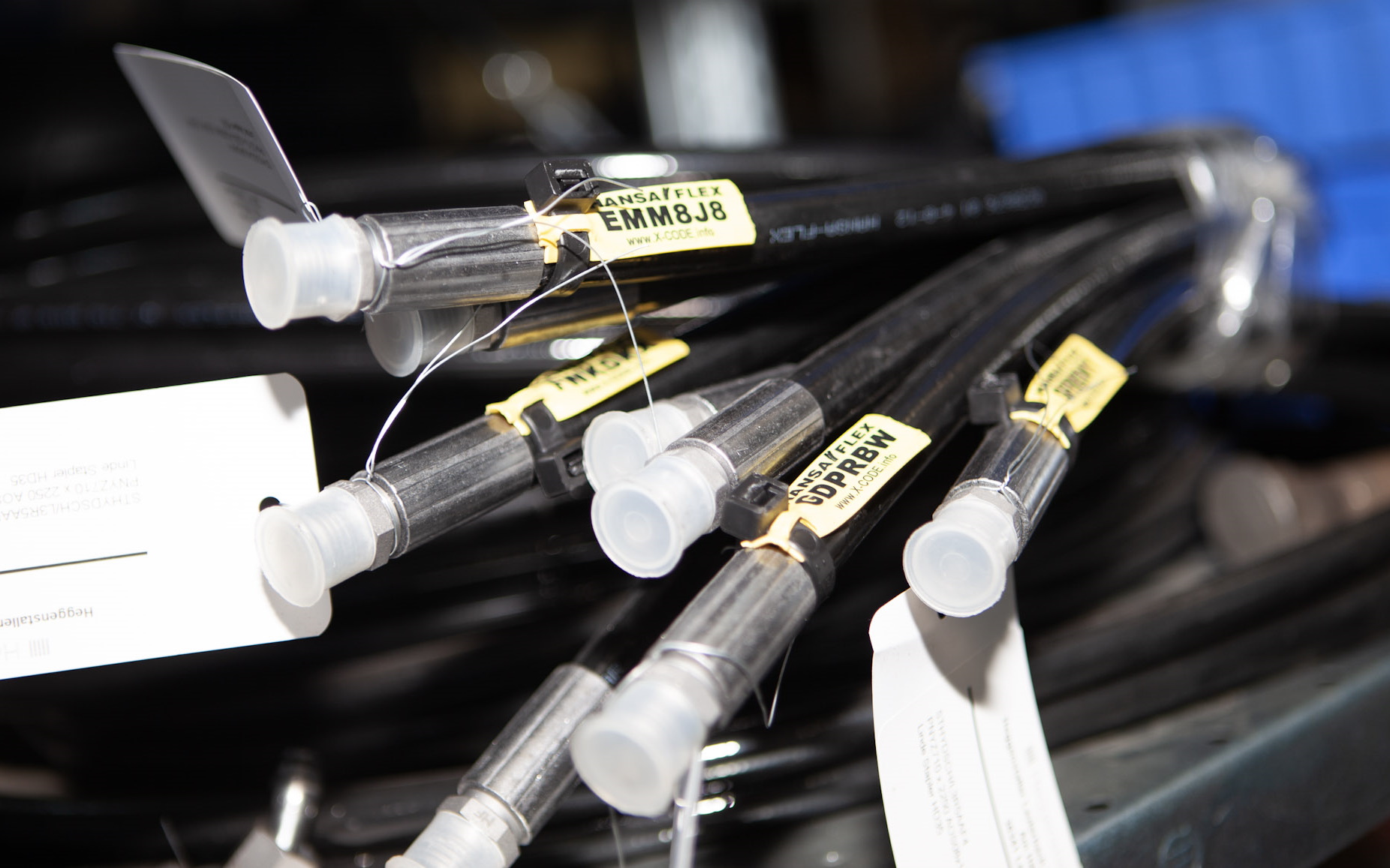
Do you have any questions about our services and products? Or do you need help?
Sundays and public holidays are excluded
Since the founding of the Pfeiffer Group's timber plant in Lauterbach in 2009, HANSA-FLEX has been the first point of contact there when it comes to hydraulics and the associated services.
No monkey business: at “Pongoland” in Leipzig Zoo, the hydraulic system has to be carefully planned and secure.
For 30 years Agrartechnik Vertrieb Sachsen GmbH has been an established name in agricultural engineering. HANSA-FLEX has accompanied this success story from the very beginning.
Since the founding of the Pfeiffer Group's timber plant in Lauterbach in 2009, HANSA-FLEX has been the first point of contact there when it comes to hydraulics and the associated services.