In this interview Axel Tammen, Head of Technology and Quality Assurance at HANSA‑FLEX, talks about the latest developments and trends in fluid technology, and explains what is already technically possible today.
How have requirements in fluid technology changed recently?
The requirements are on the increase: installation spaces are becoming smaller with tighter bending radii, weight has to be reduced and hose lines have to become more flexible. At the same time they are operating under higher pressures. We are investing more in research and development to keep pace with these developments. For example, we have been able to launch connecting elements with greater resistance to red and white rust on the market, and have increased the service life of our HANSA‑FLEX hose lines by improving their pulse resistance. Our aim is always to create products with added value for customers. Of course this is a challenging and exciting task for my team and me.
What role does sustainability play?
The energy-efficient operation of hydraulic systems is becoming increasingly important, with regard to ESG regulations, too. A lot can be achieved here with manageable effort. We demonstrated this when we retrofitted the pressure pulse test benches in our central Quality Assurance department: we integrated control units as well as new motors and pumps, so that the system only provides as much energy as is needed and doesn’t always run at peak load. This has enabled us to reduce operating costs by over 50 %. It requires comprehensive expertise, which we also use to support our customers. Our hydraulics specialists identify potential savings, suggest appropriate measures and carry them out.
What other developments are you currently experiencing?
Another focus is on environmental compatibility. In water protection areas, for example, mobile machines such as excavators need to be operated with biodegradable hydraulic oil. We carry out resistance tests to ensure that the biodegradable oil used and its additives are compatible with the rubber components of hoses and seals. The circular economy is also an important issue: our colleagues in Austria have developed a process that enables used hose lines to be recycled. We also operate test benches with electricity from our own photovoltaic system, and use heat recovery systems. Our customers also benefit from this experience.
What do you currently see as the biggest task?
We are experiencing a lot of changes in a short space of time, so it's important to stay on the ball. We’re currently testing the possibilities of additive manufacturing, in particular with regard to pressure resistance, and have produced screw connections using the 3D printing process. In the area of predictive maintenance, we’re looking to use sensors to help our customers to detect potential faults at an early stage. It’s important to know when there is a significant deviation. Within the scope of the VDMA Fluid Technology Research Fund, we are addressing such questions and investigating, for example, whether the leakage oil rate allows conclusions to be drawn about the service life of hydraulic motors.
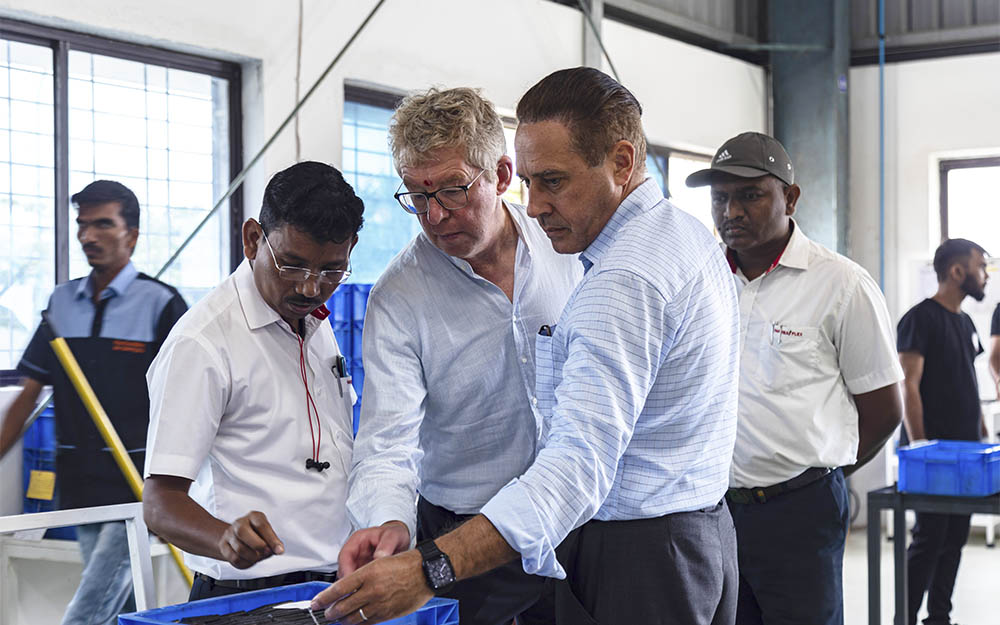
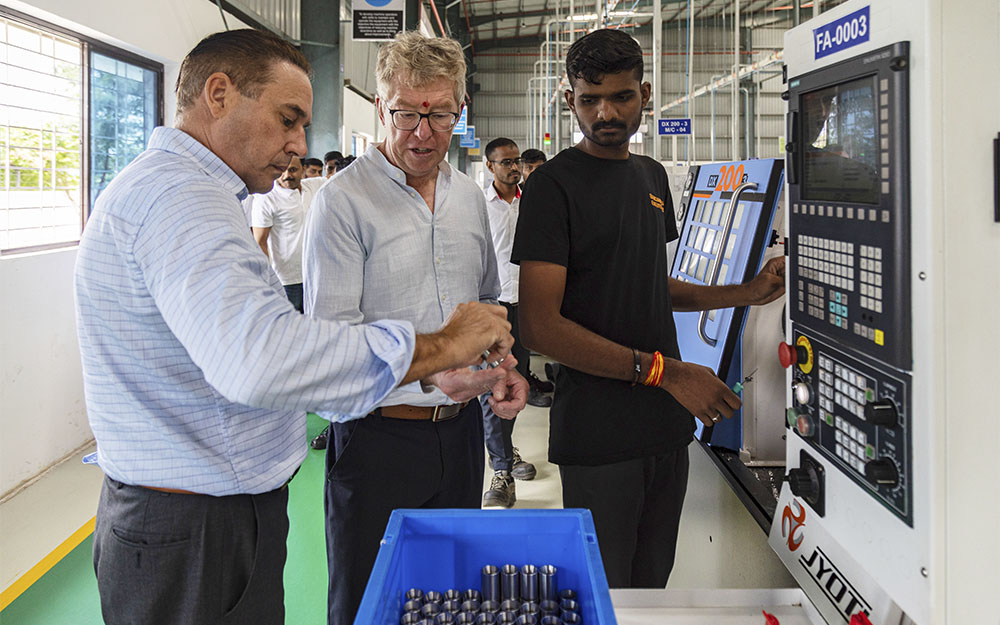
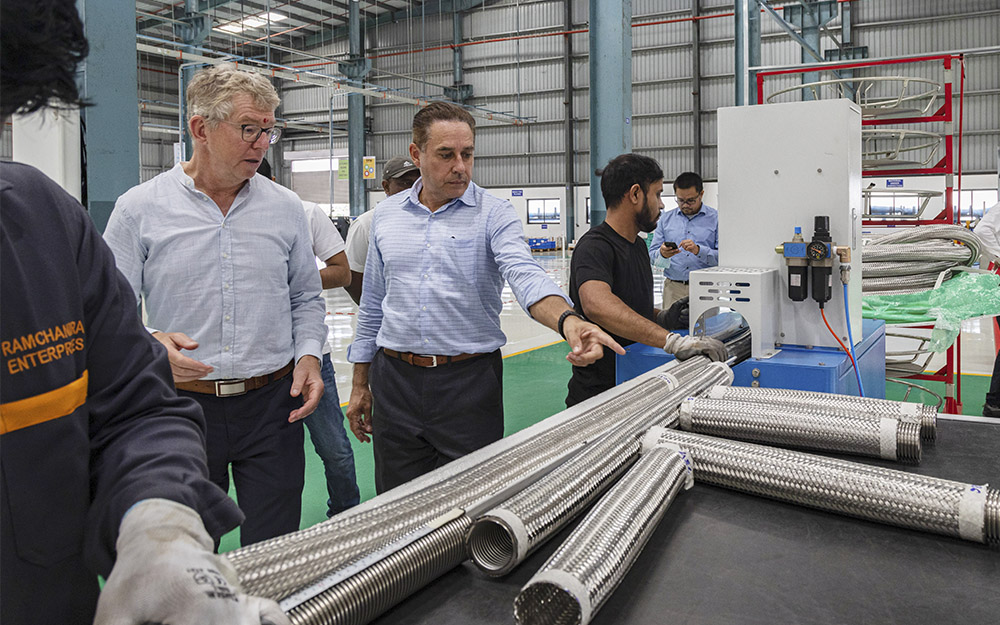
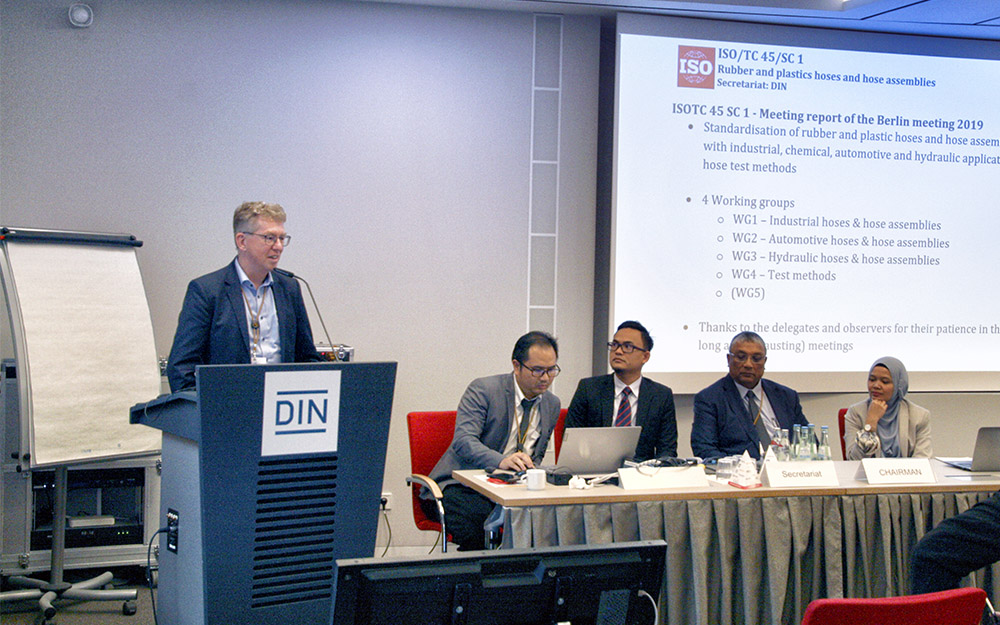
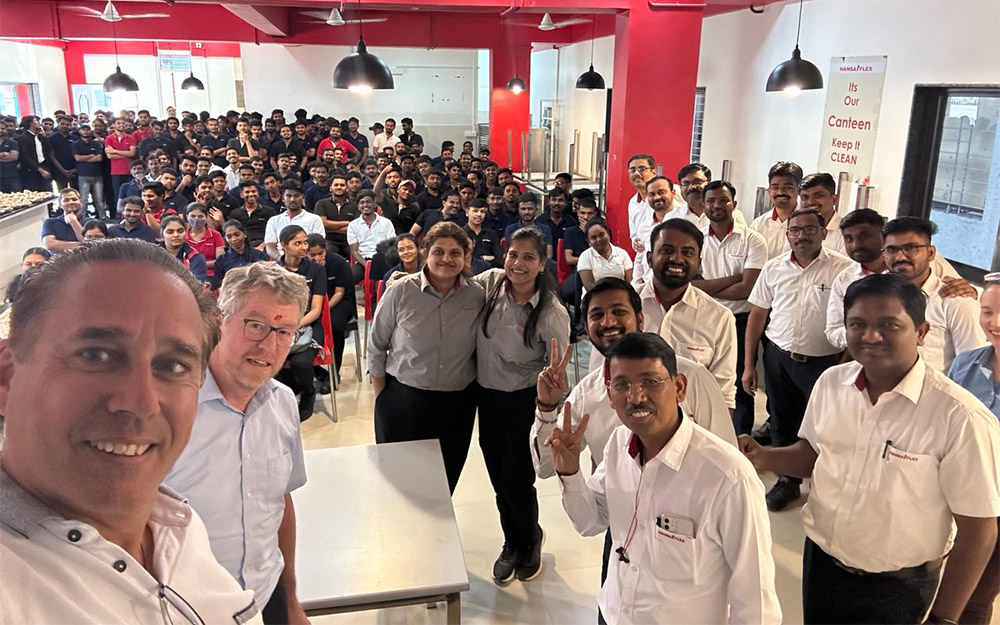
So the trend is towards networked and automated systems?
Definitely. However, a lot more groundwork still needs to be done before intelligent hydraulic systems are ready for the general market. It all starts with the data. We’ve really done our homework here: all articles are classified in our PIM system and are available as digital twins. Compatibility of components also plays a major role in system planning. For this reason HANSA‑FLEX has been involved in developing standards for many years. I’m the chairman of the ISO/TC 45/SC 1 committee with responsibility for the results of the working group on hose lines, which is working on the harmonisation of pressure ranges and recommendations for policy makers.
How do you reconcile this with your daily tasks?
If you want to make major leaps forward, you also need to take small steps. After all, if you don’t get fundamentals such as customer satisfaction right, all your visions just remain unattainable castles in the air. In our department we ensure consistently high quality, and continue to develop our products in order to exceed the requirements of the market wherever possible. Another step towards the major goal of digitalisation is improved communication between our Technology and Quality Assurance sections, which we have achieved with the move to our new shared competence centre.